Importance of Calibration Services in Manufacturing
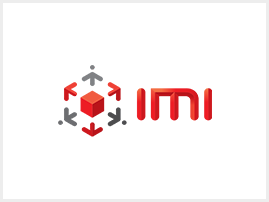
June 14,2019,Philippines—Healthy competition in the global manufacturing industry is necessary because it pushes companies to continuously improve their products in order to get ahead of their competitors, giving consumers plenty of quality choices. However, the improvements in technology along with the changing demands of consumers have only made the competition harder, especially for smaller and newer companies. As a matter of fact, only five percent of 30,000 new consumer products launched every year succeed in the market, while the rest fail according to Harvard Business School professor Clay Christensen.
Along with having a well-planned new product introduction process, doing calibration on manufacturing devices is critical in ensuring the success of the product out in the market. However, what is calibration and just how exactly is it important in manufacturing? Here are answers to some of the most common questions about calibration services in manufacturing.
What is calibration?
Even just one centimeter off in measurement can result in a faulty or low-quality product, that is why manufacturers always need to be mindful of measurement accuracy during production, and calibration services help them do that.
Calibration is the act of comparing a device under test (DUT) of unknown value with a reference standard of a known value to check if the DUT follows industry standard measurements or not. One of the simplest ways to perform a calibration is by testing the devices side by side. For example, a manufacturer may put both the DUT thermometer and a calibrated reference thermometer in boiling water to take its temperature at the same time. After calibrating the device, next would be the adjustment which is technically a separate step from calibration.
Why are calibration services important?
Calibration services are critical in global manufacturing for many reasons. Firstly, calibration checks if the measurements are taken by the DUT are accurate, and once the accuracy of the DUT is fixed according to industry standards, it helps manufacturers use only the appropriate amount of resources and raw materials for their products which then reduces manufacturing waste. Accurate measurements also help reduce the risk of producing a faulty or low-quality product which is beneficial in ensuring the safety standards of the product as well as of the consumer who will be using it.
With safer and more reliable products, the brand and company image is also protected. It reduces the chances of consumers leaving complaints and bad reviews about the product, and helps the company avoid potential financial losses from a possible boycott. In worst case scenarios, manufacturing companies may face legal charges due to an accident caused by their faulty products. Calibration will also ensure that such events would not happen.
When and how often is device calibration necessary?
Every device has a different calibration schedule. Generally, manufacturers provide information on the recommended calibration interval per device. However, one of the rules in calibration is that the more often a device is used, the more often a calibration should be done. Similarly, the more critical the measurements the device takes the more frequent the device needs calibration. For such situations, it is recommended to do monthly or quarterly calibrations.
It is also recommended to calibrate devices before and after a major critical measuring project to check and confirm the accuracy of devices. However, if the projects are non-critical, it is okay to calibrate only once or twice a year. In cases of unforeseen accidents (such as dropping the device) happening, calibration must be done as soon as possible.
Many EMS company in the Philippines and other countries around the world include calibration services in their capabilities, so finding a place to calibrate manufacturing devices would not be hard.
Calibration is more than just a process for fine tuning a manufacturing device. It is extremely important in ensuring the safety and reliability of the manufacturing device as well as of the product to be made.
Other Blog
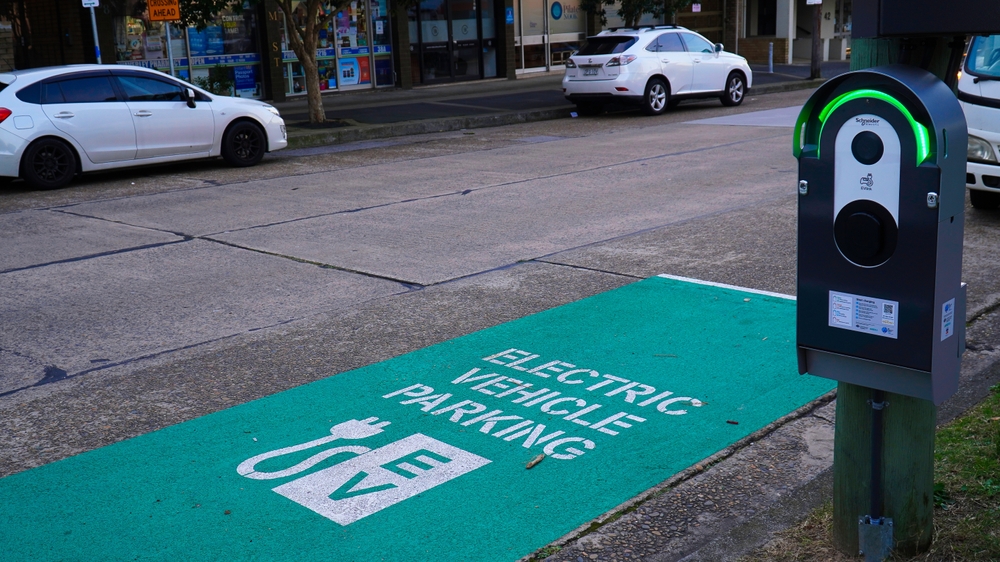
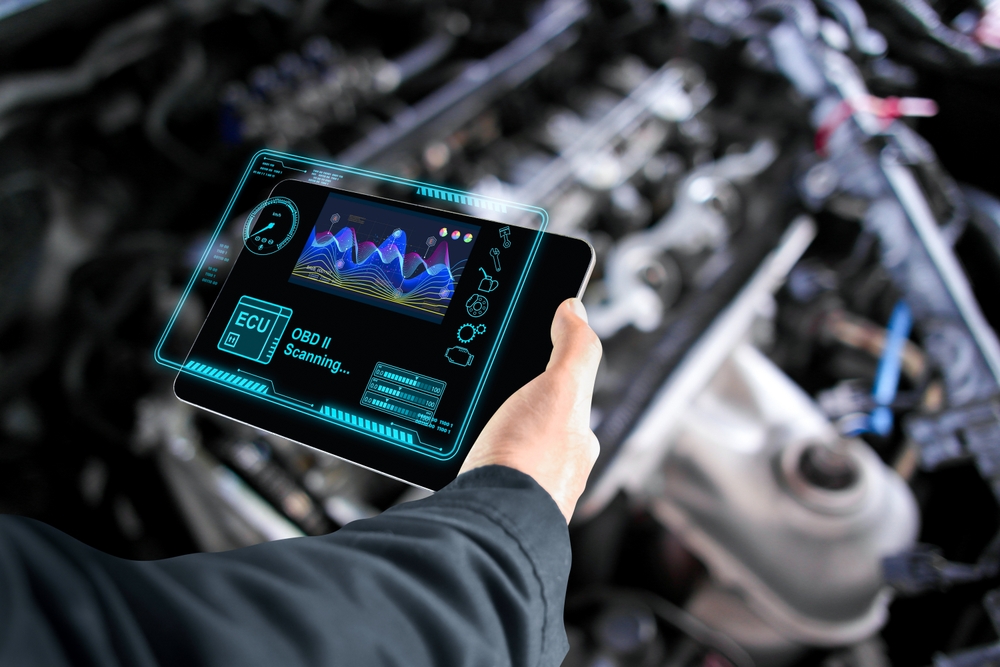