All Systems Go During “Lights Out”
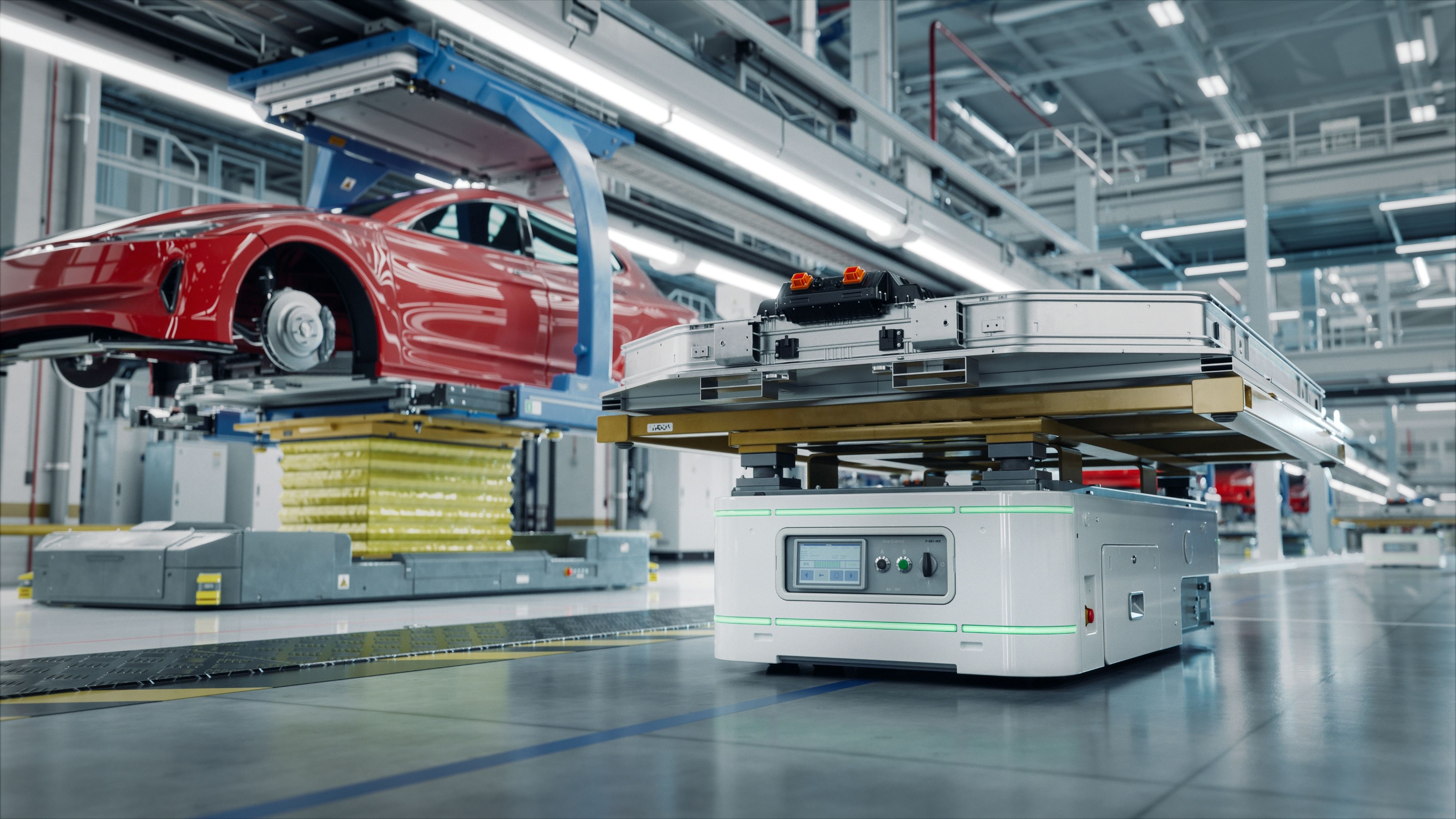
Once dismissed as a futuristic fantasy, the concept of an entirely automated, round-the-clock factory is now a practical reality. No longer limited to theory, lights-out manufacturing is proving its value on the ground, offering scalable solutions and a clear edge in today’s competitive industrial market.
Advanced automation and tool technology are no longer limited to manufacturing giants or brand-new facilities. McKinsey reports that manufacturers can increase productivity and throughput by up to 30% through strategies like lights-out operations. Gartner projects that by 2025, 60% of manufacturers will have at least two fully automated processes running in one of their factories. Despite the data, many still see lights-out manufacturing as out of reach.
Understanding lights-out manufacturing
Lights-out manufacturing refers to a production model where machines, robotics, and intelligent systems operate with minimal or no human involvement. Also known as dark factories or autonomous production, these facilities rely on advanced system integration to connect and coordinate hardware, software, and data in real time. This future-ready setup allows them to run around the clock without the need for lighting, climate control, or on-site personnel.
As businesses face tighter margins and mounting pressure to deliver more with less, lights-out manufacturing is emerging as a timely solution. The model is driven by the rise of cutting-edge manufacturing solutions such as robotics, machine vision, edge computing, and AI. Integrated into a single digital ecosystem, these tools allow precision machinery to manage everything from production and inspection to real-time adjustments.
The shift is also being propelled by external forces. Labor shortages, rising wages, and a growing skills gap are making it harder to implement factory models that offer sustainability.
Meanwhile, customer expectations for speed, quality, and traceability are intensifying. On top of that, environmental targets and stricter regulations are pushing industries toward low-waste, energy-efficient systems. Together, these pressures are making lights-out manufacturing not just viable, but essential for staying competitive.
The Tech Behind Lights-Out Manufacturing
Many of the tools driving lights-out production are already familiar in modern factories. Robots perform tasks such as fastening and part placement, while automated guided vehicles (AGVs) and robotic arms manage material flow. Machine vision handles real-time quality testing, and machine learning continuously refines performance, supporting efficient test and system development. Other technologies include:
- Digital twins
Like a virtual replica of the factory floor, digital twins enable seamless coordination by simulating processes in real time. They support automated production by predicting failures, optimizing workflows, and enhancing design for manufacturing.
- Artificial intelligence
Lights-out manufacturing builds on lean manufacturing principles by automating streamlined, waste-free processes. With AI and analytics, it pushes efficiency further, adjusting operations in real time, predicting equipment needs, and refining production.
- Industrial Internet of Things
Thanks to IIOT, live machine data and remote access are reshaping how manufacturers monitor performance and conduct reliability testing. Once-isolated equipment is now part of a connected network, where historical trends are measured against real-time data to guide smarter decisions.
- Edge & cloud integration
Edge and cloud computing deliver the speed and scale needed for lights-out manufacturing. Edge devices process data instantly, while cloud platforms enable remote access and coordination. This real-time control supports predictive maintenance and drives economic value.
(Also read: Digital Tools: Driving Factories with These Top 10 Benefits)
Top benefits of lights-out manufacturing
Lights-out manufacturing offers a range of advantages that are reshaping how modern factories operate.
- Workplace safety
Automated production reduces the need for workers to operate heavy machinery or enter hazardous areas, such as those requiring low-temperature storage. With systems handling tasks independently, exposure to physical risks drops significantly, creating a safer environment.
- Lowered costs
Faced with labor challenges and rising costs, manufacturers are turning to full automation to cut expenses. With minimal staffing, facilities save on wages, lighting, testing personnel, and climate control, particularly in low-use areas.
- Improved operational efficiency
One major advantage of full automation is improved production performance. Machines operate continuously without requiring breaks. This steady pace reduces downtime and limits quality issues, as automated systems repeat tasks with consistent accuracy every time.
- Sustainability
Automation helps reduce environmental impact by cutting energy use, material waste, and emissions. With no need to heat, cool, or light spaces for human workers, energy consumption drops. Accurate, repeatable processes also lower scrap rates and support standard compliance.
(Also read: Steps for a Greener Tech Industry)
- Agile processes
This manufacturing method supports flexible operations that adapt quickly to changing conditions. Whether responding to demand shifts or material availability, smart systems boost resilience. Real-time data from equipment controls allows manufacturers to automate based on machine health and performance.
What makes lights-out manufacturing difficult
Here are some of the key hurdles manufacturers may need to overcome when setting up a dark factory:
- Significant upfront costs
Going lights out involves major upfront spending on robotics, software, and infrastructure. These initial costs can be a challenge, especially for small and mid-sized manufacturers. Additional expenses for integration, customization, and training often delay returns, making the transition financially demanding at the start.
- Tech difficulty
Automated systems boost efficiency, but they aren’t failproof. Technical issues can bring entire operations to a standstill, causing costly downtime. Troubleshooting in an autonomous setup is complex, often requiring specialized expertise and investment, making system reliability and maintenance a critical challenge for manufacturers adopting this model.
- Limited capabilities
This setup works best for high-volume, repetitive tasks. In contrast, complex processes or small production runs may not justify the cost or effort. Self-operating systems are often built for fixed operations and may struggle to adapt to product changes or customization demands without costly reprogramming.
Conclusion
Despite its challenges, lights-out manufacturing remains a worthwhile pursuit for companies aiming to stay competitive in a rapidly evolving industry. While high upfront costs, technical complexity, and limited flexibility can slow adoption, the long-term benefits offer a strong return on investment.
With careful planning, phased implementation, and strategic investment, the shift toward lights-out operations can help businesses streamline production, increase uptime, and build resilience in the face of workforce gaps and growing business demands.
As one of the Top 20 EMS companies in the world, IMI has over 40 years of experience in providing electronics manufacturing and technology solutions.
We are ready to support your business on a global scale.
Our proven technical expertise, worldwide reach, and vast experience in high-growth and emerging markets make us the ideal global manufacturing solutions partner.
Let's work together to build our future today.
Other Blog
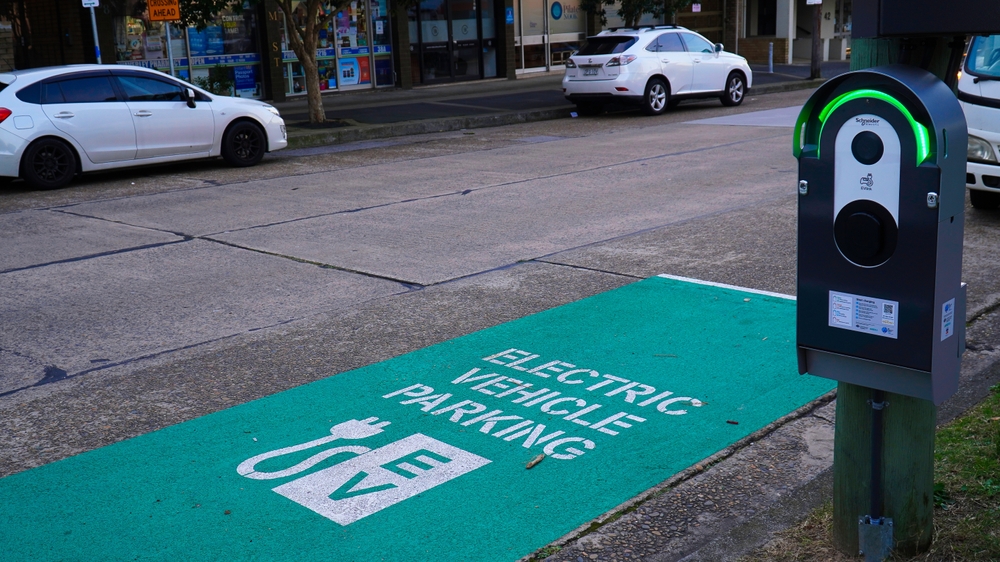
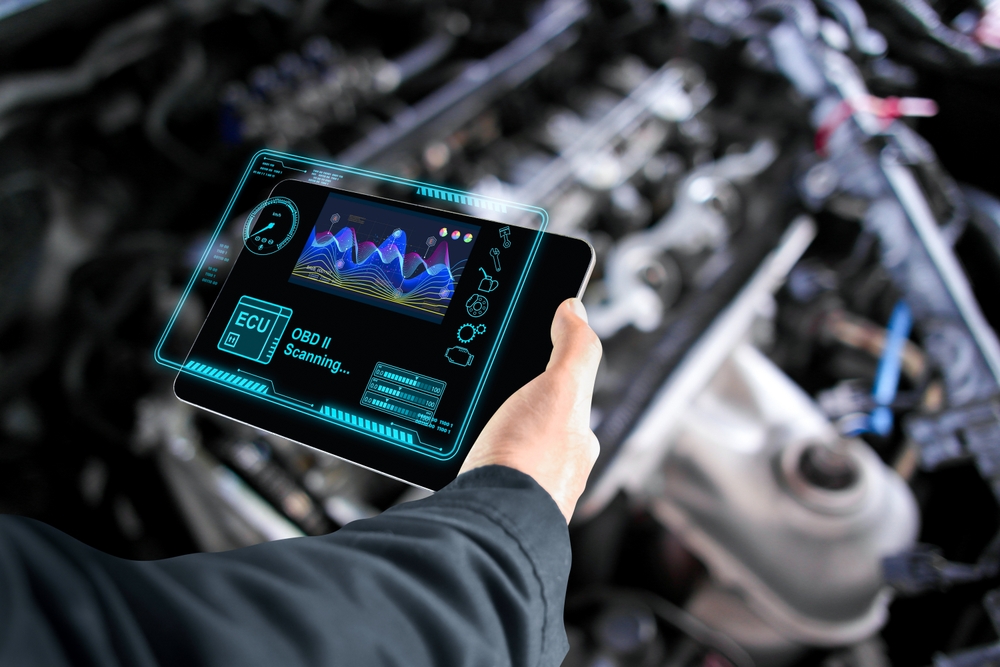