Top Tech Tools to Take Your Manufacturing to the Next Level
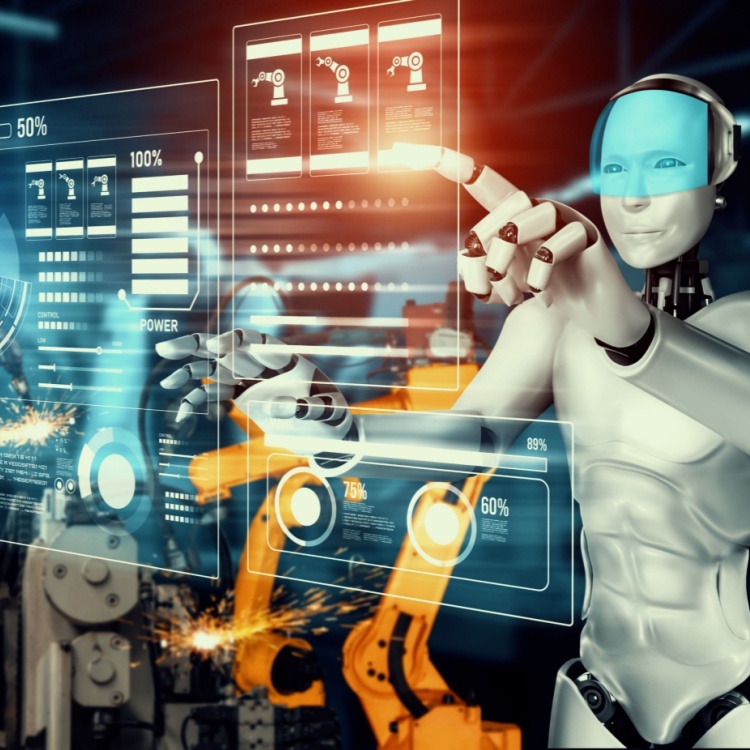
Manufacturers are adopting digital tools and automation to replace traditional processes, offering significant gains such as 10 to 30% higher production throughput, 10 to 20% lower quality costs, and up to 50% less downtime. Despite these advantages, only about one-third of companies have moved beyond early implementation, largely due to limited understanding. This article highlights the transformative potential of digital technologies, outlining their benefits and industrial manufacturing solutions.
Smart factories represent the next generation of manufacturing facilities, integrating advanced technologies to create fully connected and automated environments. These factories collect and analyze data in real-time, bridge physical and digital operations, and enhance productivity while ensuring future-proof processes and responding swiftly to changing market demands.
As manufacturing evolves, smart factories play a pivotal role in shaping its future by driving innovation and resilience. With their ability to adapt and optimize processes continuously, smart factories are not only transforming how products are made but also fostering manufacturing excellence in a rapidly advancing digital economy.
Top 10 tech tools in manufacturing
Here are the cutting-edge technologies driving the digital transformation of manufacturing, helping businesses enhance efficiency, innovation, and competitiveness.
-
3D printing
3D printing, or additive manufacturing, is revolutionizing the manufacturing sector by enabling the creation of complex parts and products on demand. Ideal for product testing, limited-run production, and personalized designs, it reduces production time and costs while offering high precision. This technology is transforming industries like healthcare and aerospace engineering, as well as the automotive market.
-
Robotics
Robotics and collaborative robots (cobots) boost global manufacturing by enhancing precision, reducing defects, and enabling 24/7 operations. Integrated with other tools like analytics, these technologies improve operational efficiency and create adaptive systems. Cobots excel in packaging and assembly, swiftly learning tasks, handling dull or dangerous jobs, and freeing employees for more rewarding roles.
-
5G
5G is set to transform electronics manufacturing services (EMS) by providing high-speed, low-latency connections crucial for smart factories. This advanced connectivity accelerates data transmission, enhances uptime, and supports net-zero goals. With unmatched speed and versatility, 5G empowers innovation across all production stages, addressing the sector’s most pressing challenges.
-
Artificial intelligence (AI)
AI boosts precision machinery operations in smart factories through predictive maintenance, quality control, and efficient scheduling. AI schedulers optimize costs and reduce changeover times, while predictive maintenance prevents equipment failure, enhancing productivity. A study revealed this approach increases factory uptime by 10 to 20%, showcasing AI’s ability to impact manufacturing across industries.
-
Machine learning (ML)
This technology uses predictive algorithms to assess production data, optimize workflows, and predict failures. Through power cycling, it adjusts actions in real time, refining schedules based on demand and resources. By integrating AI and ML, manufacturers streamline supply chains and improve quality control with minimal human intervention.
-
The Industrial Internet of Things (IIOT)
IIOT connects smart sensors and devices to streamline manufacturing through data collection and analysis. By providing real-time insights, this efficiency, supports sustainability with energy management, and strengthens supply chain traceability. This technology fosters smarter business decisions, transforming industrial operations with advanced analytics.
-
Cloud computing and edge computing
Cloud services provide scalability, cost savings, and efficiency, enhancing supply chain management and fostering innovation in design and engineering. Meanwhile, edge computing processes data locally, improving response times and bandwidth, and delivering real-time insights and predictive analysis to improve operational performance.
-
Digital twins
Digital twins are virtual replicas of physical systems, enabling real-time monitoring and optimization in smart manufacturing. They collect sensor data to detect issues, improve forecasting, and simulate scenarios. Used for tasks like leakage tests, thermal analysis, and material testing, digital twins help manufacturers optimize production, reduce costs, and enhance product quality through predictive insights and efficient simulations.
-
Extended reality (XR)
XR technologies, including virtual reality (VR) and augmented reality (AR) enhance training and product development. VR creates immersive simulations for employee training, improving skill retention and reducing errors. Meanwhile, AR overlays digital information onto the physical world, assisting workers with real-time data. Both technologies facilitate efficiency and better communication.
-
Cybersecurity
As manufacturing embraces digital transformation, enhanced connectivity improves workflows and productivity. However, this digital shift also exposes the industry to increased cyber risks. In 2022, manufacturing was the most cyber-attacked sector. Despite its potential, the industry remains relatively unaware of the security vulnerabilities associated with connected technologies, highlighting the need for robust cybersecurity measures.
Benefits of digital transformation for manufacturing
Digital transformation is reshaping the manufacturing landscape, driving advancements in automation, data analytics, and connectivity. These shifts are poised to redefine competitive strategies in the sector, offering these benefits:
-
Streamlined operations
Digital tools boost operational efficiency through automation, predictive maintenance, and optimized resource utilization. Automation streamlines production, reducing errors and downtime while ensuring timely repairs. Advanced analytics also minimizes resource consumption, lowering production expenses and carbon emissions.
-
Reduced costs
Digital transformation can reduce production costs by up to 70%, with most companies seeing cuts between 15% and 30%. Improved equipment efficiency, optimized scheduling, and faster issue detection contribute to better operations and increased profitability.
-
Increased productivity
With new technologies, manufacturing enjoys better productivity, with many factories doubling output. Key factors include optimized line balancing and reduced micro stops. Precision manufacturing, rapid prototyping, and customized production enhance product quality, innovation, and market responsiveness, giving manufacturers a competitive edge.
-
Workforce efficiency
Manufacturers can improve labor efficiency by 15% to 30% through automation and advanced technologies. Reducing manual tasks frees workers to focus on value-added activities, while AI tools enhance visibility and enable better labor allocation. Data-driven performance reports optimize scheduling and workforce utilization.
-
Improved forecasting
Digitalization boosts forecasting accuracy for manufacturers by up to 85%, leveraging advanced planning systems and real-time data on material flow, capacity usage, and schedule adherence. Machine learning models enhance predictions, optimizing supply chain management and boosting workflows.
-
Sustainability
By leveraging sustainability software like carbon trackers, manufacturers can reduce CO2 emissions and water consumption by around 15%. These technologies enable real-time monitoring, driving data-based decisions that minimize waste and optimize energy usage, contributing to reduced environmental impact.
-
Customer satisfaction
Digital transformation helps manufacturers speed up delivery times, promoting supply chain transparency, and increasing responsiveness to customer needs. Technologies ensure product quality and origin, while digital systems allow manufacturers to adjust production in real-time based on feedback.
-
Enhanced supply chain management
A digital supply chain enhances collaboration and transparency across teams. Real-time data enables seamless communication, allowing manufacturers to stay ahead of potential disruptions. Integration with suppliers ensures smoother planning, while AI-driven insights help maintain clarity throughout production, fostering stronger, more effective partnerships.
Despite the advantages, challenges remain in fully realizing the potential of digital transformation, including these issues:
Despite the challenges, digital transformation is still worth pursuing. It enhances efficiency, quality, and sustainability while making your business more resilient. By leveraging comprehensive data and streamlined processes, manufacturers can better anticipate disruptions and ensure long-term growth, positioning themselves as adaptable leaders in the competitive market.
As one of the Top 20 EMS companies in the world, IMI has over 40 years of experience in providing electronics manufacturing and technology solutions.
We are ready to support your business on a global scale.
Our proven technical expertise, worldwide reach, and vast experience in high-growth and emerging markets make us the ideal global manufacturing solutions partner.
Let's work together to build our future today.
Other Blog
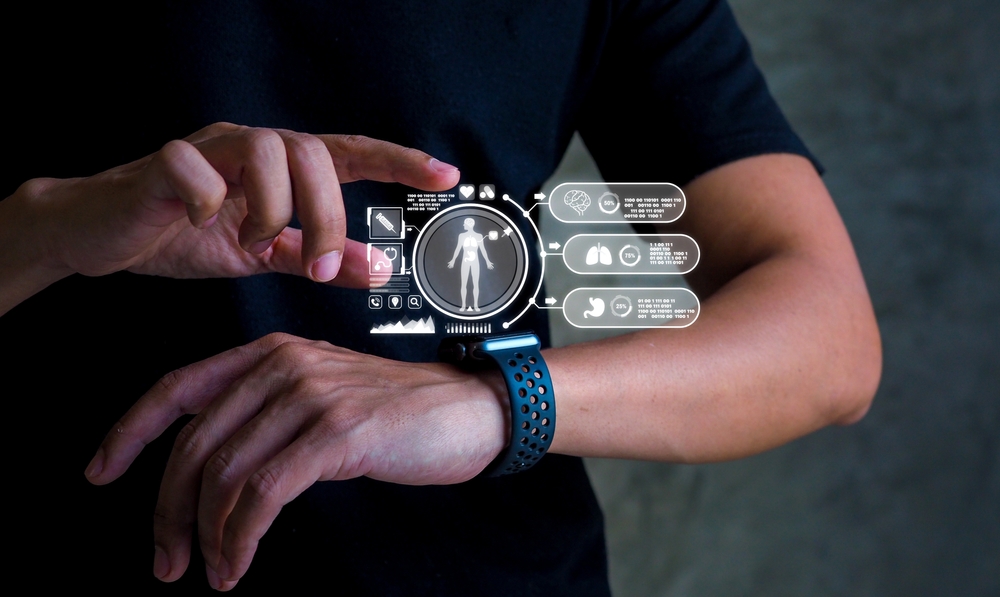
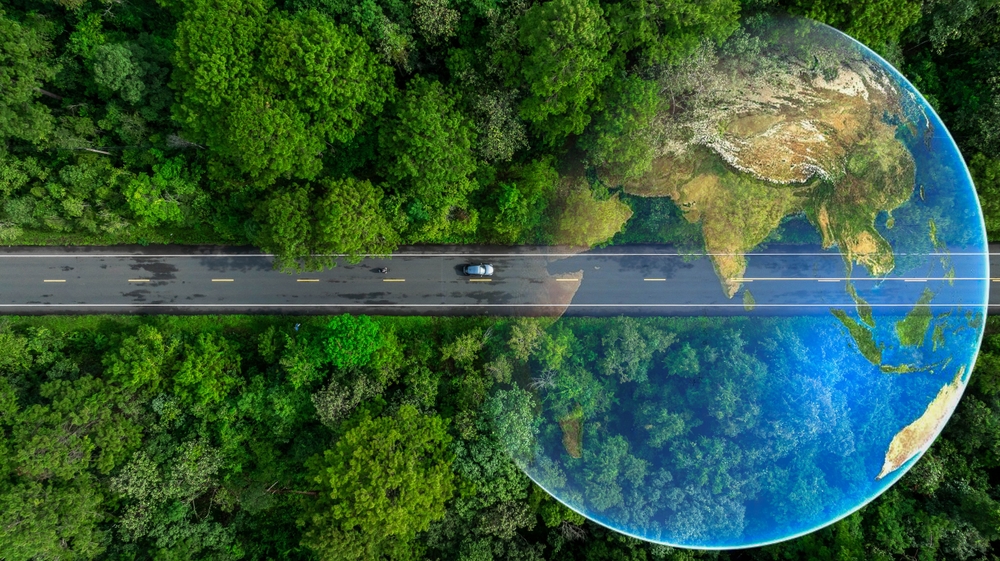
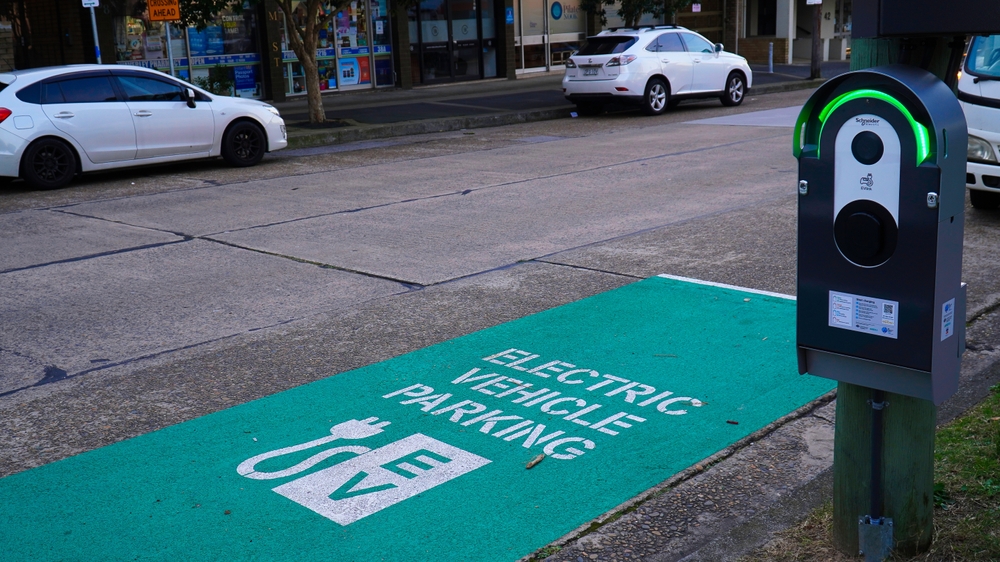