How 3D Printing Breaks Manufacturing Rules in the Best Way
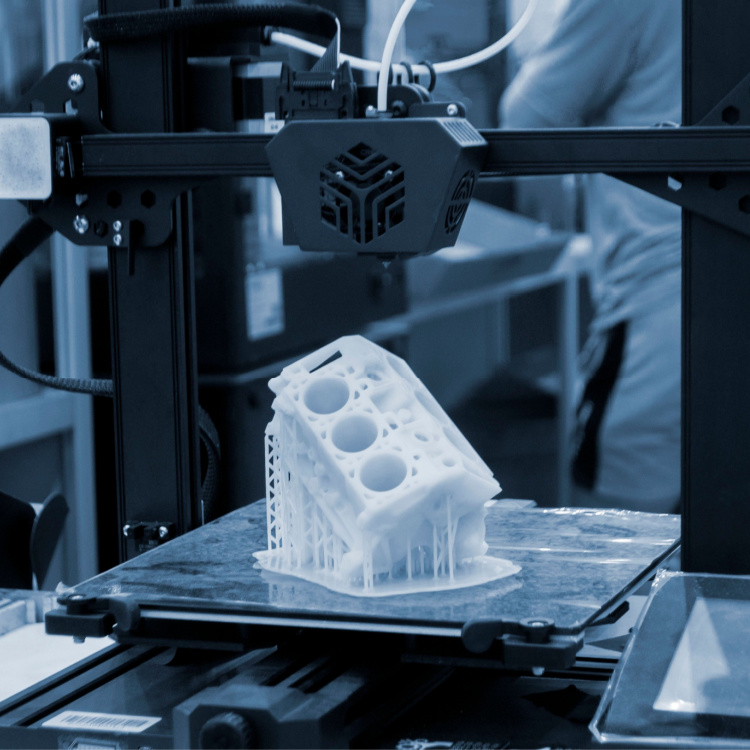
Additive manufacturing is elevating how products are made by allowing limitless freedom in design.
Manufacturing has come a long way from using traditional methods such as manual machining, injection molding, and even CNC (computer numerical control) machining. These practices have dominated the manufacturing industry for decades, setting the standard for making everyday tools and electronic devices.
However, in the last eight years or so, additive manufacturing has become a game-changer not only in manufacturing but in many industries, especially in automotive and electronics.
Although the first 3D printer came out in 1981, its massive potential has only recently emerged. From firearms to buildings, is there anything 3D printers can’t print?
(Also read: It’s a Bold New 3D Printed World)
3D printing is part of additive manufacturing, and it is very distinct from traditional means of manufacturing. It involves creating components layer by layer, instead of by sculpting components from a source material, which is how machining works. On the other hand, injection molding creates components via liquid being poured into a pre-made mold and allowing this to solidify.
Effective as these methods may be (or once were), machining and injection molding have many limitations, especially design-wise. It takes multiple nuts and bolts to hold things together. Many of the tools we use daily are the way they are because of design and manufacturing restrictions.
With the birth of additive manufacturing, these limitations are growing smaller by the year.
How Additive Manufacturing Frees Design
Complex shapes, ergonomic design, and organic geometries have become the trend. Before this, many tools and gadgets we use were limited to certain shapes and sizes and fit strict design standards. Customization was rare, and everyone had to work with whatever form or shape a product took. Options for sizing and function were limited before additive manufacturing.
Additive manufacturing has freed engineers and designers from the constraints and rules of conventional manufacturing because it changed the game of how components are made, making those unwieldy nuts and bolts unnecessary.
For example, piping can be a complex creation of multiple metal parts, fastened together with hundreds of fixtures. Additive manufacturing improves how this is done through parts consolidation. By reducing dozens of parts into one single piece, eliminating the need for fasteners such as screws or bolts. Instead of heavy metals, polymers are used, which are lighter but just as durable.
Internal channels such as those found in pipes are also improved with additive manufacturing. It has an edge over injection molding as it builds in multiple axes at the same time so that internal channels are built with more ease and efficiency.
“Lightweighting” is one way that additive manufacturing demonstrates more freedom in design. A great example of this is in the aeronautics industry and how brackets for aircraft are made. These are conventionally machined, which means that the brackets use more material than is needed for them to work.
Through topology optimization software, the design of these brackets can be improved. Excess weight can be shaved off from the design, giving the bracket a less bulky, and more streamlined look. Conventional machining or CNC machining may not be able to handle the newer, complex shape of these brackets but 3D printers can.
Customization is something many people have come to appreciate with the products they purchase. The feeling of acquiring something that has been specially designed to suit specific needs, and is created to make particular tasks easier for a person is highly valued in today’s world. The more targeted the need, the more specific the design.
Many modern devices that help people with disabilities would not be possible without additive manufacturing. For example, the design of prostheses has vastly improved. Every limb can now be made especially for one person. A “one-size-fits -all” solution is no longer good enough, and consumers are waking up to the realization that products could always be improved to cater to needs that are unique and can vary from person to person.
Additive Manufacturing in the EMS Space
In electronics and EMS, additive manufacturing has freed design constraints around many of our modern devices. Game controls, for example, have become sleeker, lighter, more responsive, and more comfortable than the bulky controllers of the eighties. A lot of the newer designs are thanks to additive manufacturing.
Its most significant contribution to the EMS space is designing PCBs. Circuit boards today are no longer flat and 2-dimensional. DFM (design for manufacturing) concepts have evolved since. Additive manufacturing has improved how the tiny wires inside our favorite electronic gadgets are placed to enhance the device’s look and performance.
Additive manufacturing allows for wires and conductors to be placed on curved surfaces without the danger of short circuits.
The Future of Additive Manufacturing
Many in the manufacturing space anticipate even newer applications and more innovations of 3D printing. Trends are being watched closely for where additive manufacturing can take industries such as automotive, aeronautics, medical, retail and luxury spaces.
As we become more obsessed with owning sleeker, lighter devices, additive manufacturing brings tinier and more portable components being designed and created. Innovations in polymers in 2023 include meeting the challenges of creating things measured in micrometers. Optimization is still the focus, and hybridized manufacturing systems are also much anticipated.
Because there seems to be no limit to what additive manufacturing can do, it’s an exciting area of manufacturing to keep tabs on, especially when it comes to design.
As one of the Top 20 EMS companies in the world, IMI has over 40 years of experience in providing electronics manufacturing and technology solutions.
We are ready to support your business on a global scale.
Our proven technical expertise, worldwide reach, and vast experience in high-growth and emerging markets make us the ideal global manufacturing solutions partner.
Let's work together to build our future today.
Other Blog
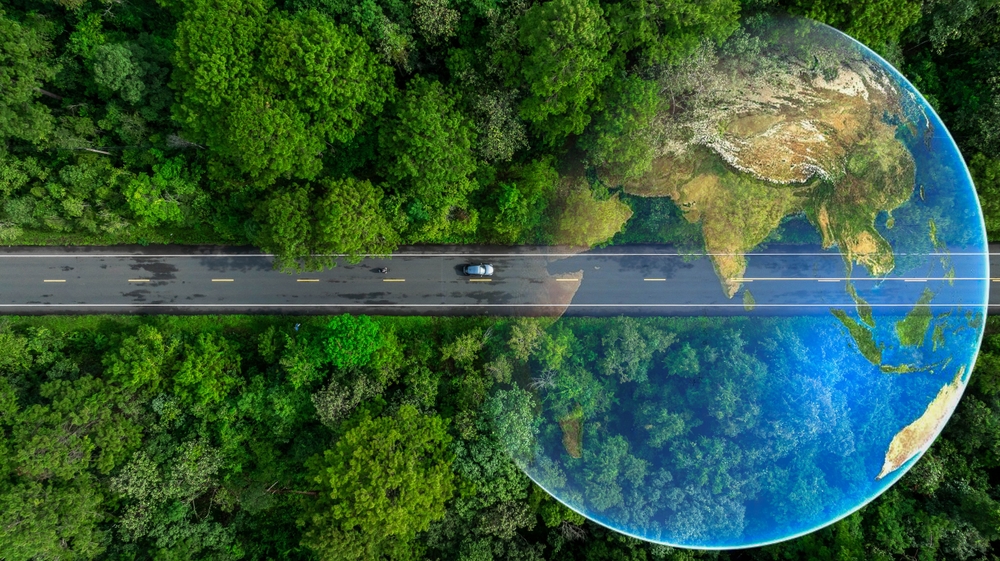
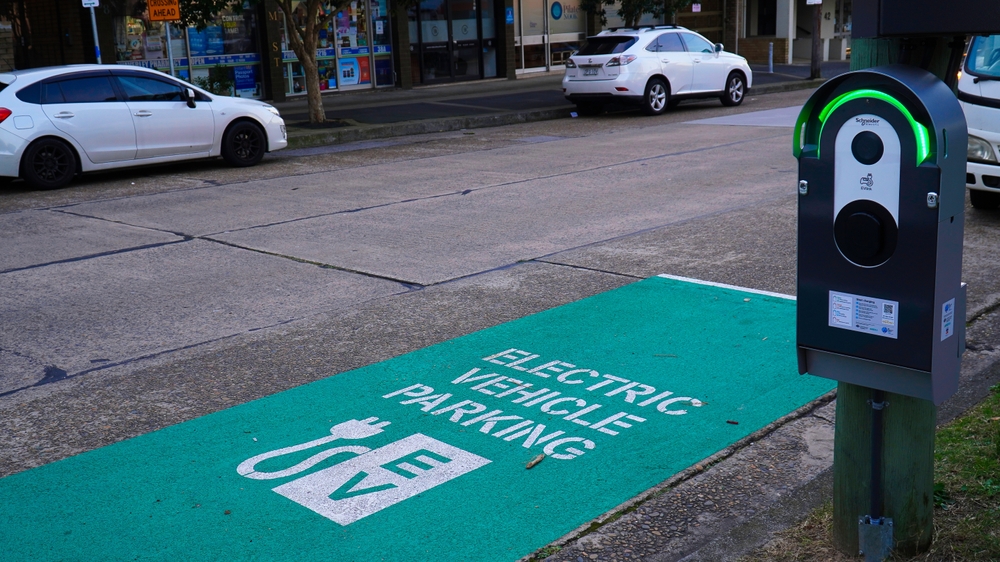
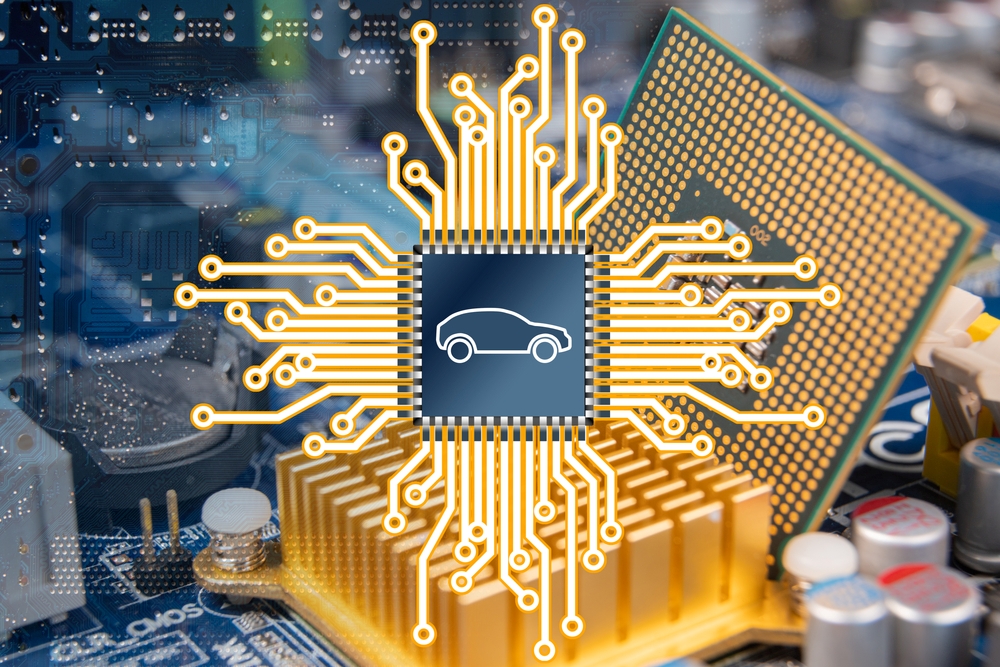