The Latest News on Smart Factories
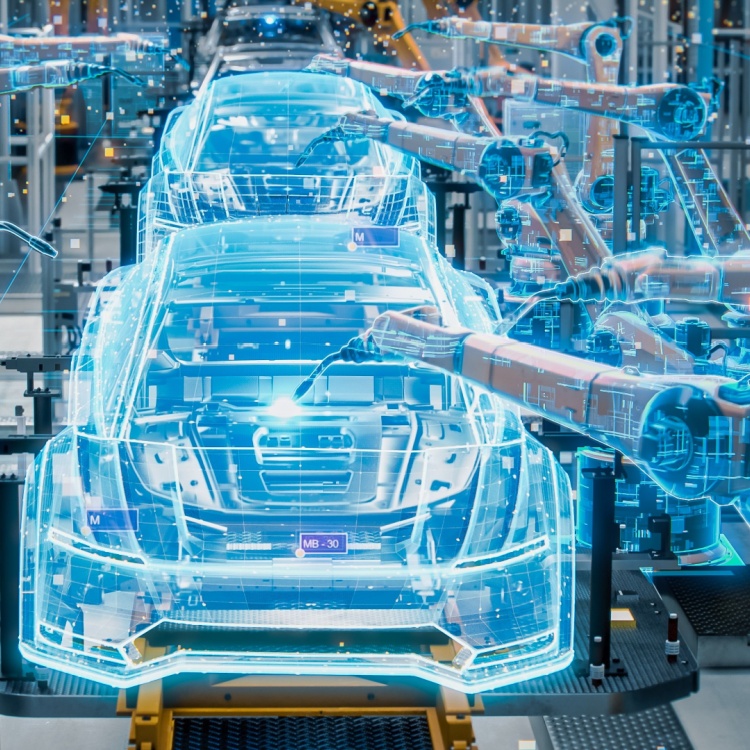
The Software-Defined Factory (SDF) revolutionizes manufacturing by using advanced software to separate production processes from hardware constraints. This approach improves operational efficiency, enabling smarter, real-time operations that can scale easily. By focusing on software-based control and coordination, SDF transforms factory workflows, offering greater flexibility, efficiency, and adaptability to meet modern production demands.
The software-defined factory (SDF) offers a modern alternative to the traditional hardware-focused manufacturing model. By relying on advanced software and APIs (application programming interfaces), SDFs allow different technical systems to communicate and work together seamlessly. This integration makes factories more scalable and cost-effective, adapting easily to new manufacturing technologies and industries.
With software managing key processes, SDFs help businesses future-proof their operations while staying flexible in a constantly changing market.
What makes up a software-defined factory?
SDFs use key technologies to make industrial manufacturing smarter and more efficient. These technologies work together to create a system that separates physical machines from the production process, making it easier to manage and improve operations.
-
Industrial Internet of Things (IIoT)
Manufacturing solutions rely on IIoT devices, which add smart connectivity to machines, tools, and production lines. These devices use sensors and communication systems to collect and share real-time data. Key communication protocols, like MQTT (Message Queuing Telemetry Transport) and OPC UA (Open Platform Communications Unified Architecture), help machines talk to each other and control systems, creating a smooth flow of information.
-
Edge computing
This tool makes quick decisions possible on the shop floor by enabling real-time data through reduced latency and bandwidth requirements. With traditional cloud setups, data still needs to be processed by a centralized server. However, with edge computing, local devices can analyze, filter, and maximize data straight from the source. As a result, the system is more responsive, able to adjust in real-time with manufacturing solutions and accomplish time-dependent duties.
-
Cloud computing
SDF’s strength is its capacity to digitize regulation systems and industrial functions in the cloud. Manufacturing industries have become familiar with customizable and agile cloud-native technologies. Instead of networks tied down to hardware, these functions can now be controlled, adjusted, and sustained regardless of physical equipment. This lets manufacturers keep track of production from anywhere while effectively allocating resources, coordinating supply chains, and ensuring close collaboration across departments, including design and engineering.
-
Digital twins
Digital twins are virtual duplicates of concrete manufacturing systems, products, or procedures. These can be utilized in various aspects—from equipment components to complete assembly lines. Manufacturing markets are realizing the benefits of digital twins, which can conduct the thorough testing of products, machine collaboration, and workflows before they are carried out in real life. Businesses can also use digital twins for predictive maintenance and operation optimization.
-
Artificial intelligence (AI) and machine learning (ML)
The backbone of an SDF’s smart automation lies in AI and ML, which also improves decision-making based on data, whether they’re historical or real-time. These tools boost manufacturing capabilities from product design and development to actual rollout. Enhanced operations due to constant feedback, early issue detection, reliability testing, and other benefits reduce both production costs and time to market.
E-FOREST: Revolutionizing Manufacturing with Software-Defined Vehicles
The latest news in the manufacturing industry highlights Hyundai Motor and Kia’s ambitious E-FOREST initiative, which aims to transform manufacturing systems through cutting-edge automation, AI, and human-friendly technologies. Designed as a smart factory ecosystem, E-FOREST will become a hub for producing software-defined vehicles (SDVs), leveraging data connectivity and digital transformation to address customer needs.
Central to this vision is the SDF, which promises shorter production preparation times, faster output, and reduced costs, ensuring superior quality in vehicle production. As the SDF matures, it will further enhance flexibility and data-driven decision-making, setting a new standard for global manufacturing.
The automakers recently held E-Forest Tech Day, a platform to foster innovation and collaboration among Hyundai Motor Group companies, partners, and startups. The event featured over 200 advanced manufacturing technologies, including the following:
-
Logistics AMR Navigation Control Software
This software helps robots move more efficiently by handling all the commands they need. Unlike older systems that only allow straight movement, the Logistics AMR Navigation Control Software lets robots move in any direction. By controlling the wheels individually, the robots can easily turn and navigate curves even while carrying heavy loads, making them much more flexible and useful for logistics tasks.
-
Atypical Flexible Parts Assembly Technology
Utilizing AI, this tech helps robots handle tricky parts like hoses and wires that don’t have fixed shapes. The AI spots the parts, figures out where to grab them, and tells the robot what to do. This is a big step for factories, as it makes automation easier and prepares them for humanoid robots in the future.
-
Infinite Multi-Axis Holding Fixture
This innovation makes factories more flexible by letting one fixture handle different parts like doors, hoods, and wheels. Instead of needing a separate fixture for each automotive part, this system adjusts automatically when the part info is updated on a computer. This saves money on fixtures and speeds up assembly by adapting to changes without extra equipment.
-
SPOT! Industry-Wide Solution
This tech tool uses a robot dog with AI, vision tech, and big data to inspect factories in real time. Equipped with sensors like "eyes," "nose," and "mouth," it checks safety and equipment conditions. This smart system helps factories catch problems early, making operations safer and more efficient.
-
UAM Wing to Body Automated Alignment System
This technology, which specifically caters to urban air mobility (UAM), automates the precise assembly of heavy UAM bodies and wings, achieving accuracy within 0.025 mm. Since UAMs need far greater precision than cars, this system meets those demands while speeding up the process from days to hours. It’s a game-changer for efficiently building advanced aerial vehicles.
By enabling flexibility, automation, and data-driven judgment, SDF redefines efficiency and adaptability. Initiatives like Hyundai’s E-FOREST integrate these innovations, showcasing real-world applications that accelerate output, lower costs, and set a new benchmark for global manufacturing in an increasingly digital and connected era.As one of the Top 20 EMS companies in the world, IMI has over 40 years of experience in providing electronics manufacturing and technology solutions.
We are ready to support your business on a global scale.
Our proven technical expertise, worldwide reach, and vast experience in high-growth and emerging markets make us the ideal global manufacturing solutions partner.
Let's work together to build our future today.
Other Blog
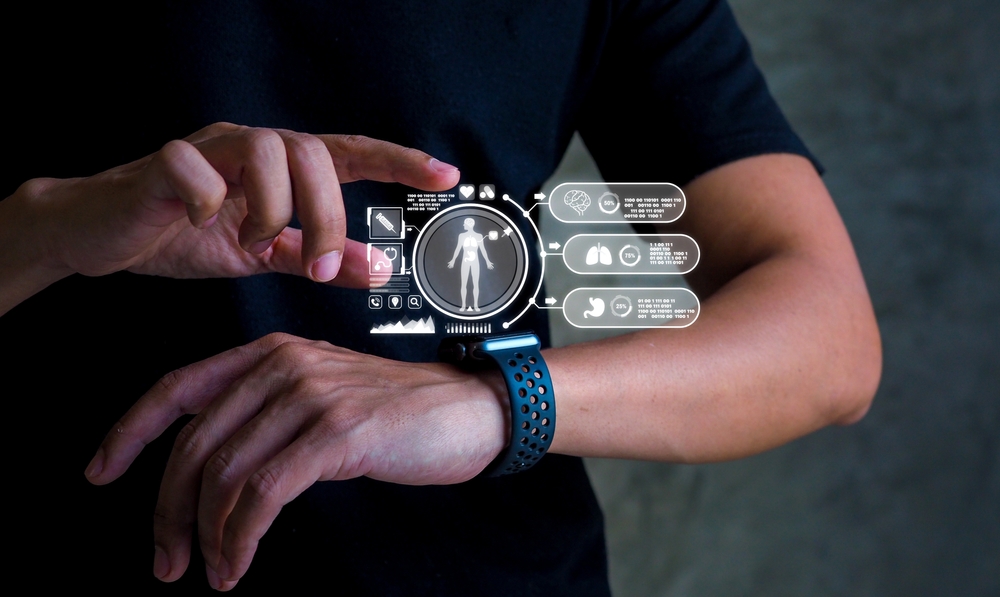
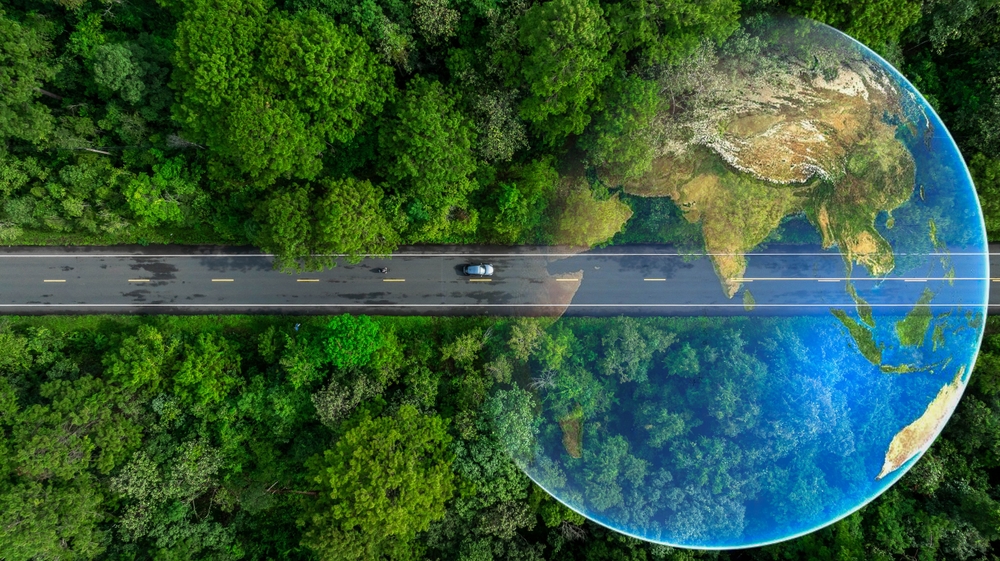
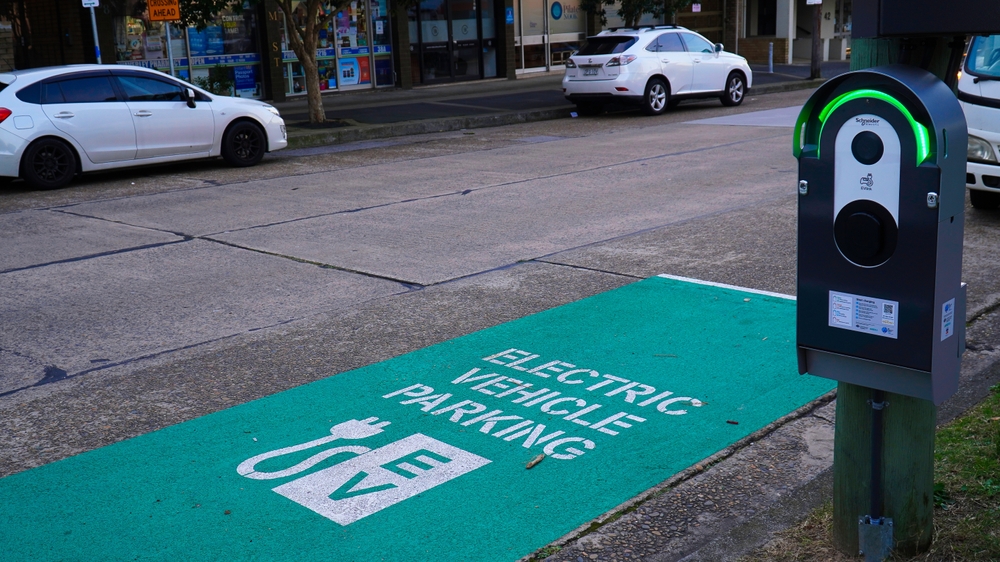