Digital Tools: Driving Factories with These Top 10 Benefits
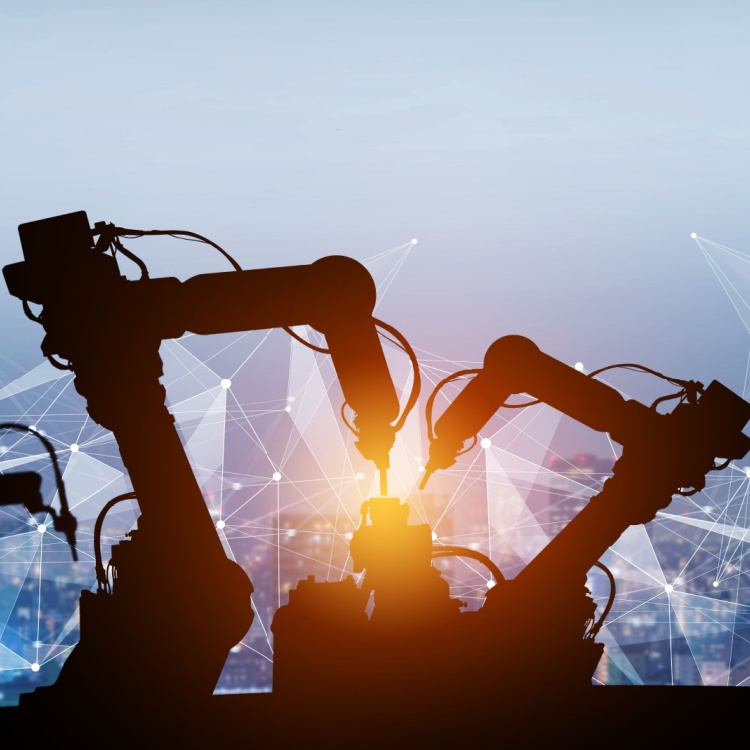
Tech-powered solutions streamline operations, cut expenses, and elevate customer experience. Studies reveal that digital advancements boost product quality and delivery speed, increasing satisfaction by 20 to 30%. Additionally, businesses leveraging digital transformation see a 15 to 20% drop in costs, thanks to enhanced efficiency and smart systems.
Manufacturers have been improving productivity and reducing waste by adopting lean manufacturing strategies. However, with the complexity and volume of production tasks, identifying areas for process optimization can be challenging.
At this point, integrating advanced technology becomes key to making global manufacturing future-ready. As demand grows and supply chain management becomes complex, leveraging modern solutions helps companies adapt to shifting market conditions and operational challenges.
(Also read: EMS Will Achieve Greater Heights: Here’s Why)
10 Game-Changing Benefits of Digital Transformation in Manufacturing
Embracing digital transformation unlocks advanced manufacturing solutions that increase competitiveness in an ever-evolving industry.
-
Improved exposure and reach
A strong digital presence is essential in today’s manufacturing markets. Implementing search engine optimization (SEO) tactics and utilizing social media can enhance website visibility and attract the right audience. Additionally, a well-structured, user-friendly website keeps visitors engaged, increasing the chances of converting them into loyal customers.
-
Positive customer experiences
Delivering seamless customer experiences is crucial for lowering acquisition costs in manufacturing industries. With 50% of manufacturers noting increased demand for faster service, AI chatbots and customer relationship management (CRM) systems enhance efficiency, reduce errors, and improve collaboration. These help businesses attract new customers while strengthening existing relationships.
-
Greater brand visibility
Building a strong brand in industrial manufacturing requires a unique identity and active engagement. Strategic content marketing differentiates businesses from competitors, while social media interaction fosters client retention. Consistent, meaningful engagement helps establish trust, making companies more recognizable and influential.
-
Revenue growth
In the industrial market, digital platforms play a key role in business expansion. Targeted ads and lead capture tools attract potential buyers, while e-commerce simplifies transactions and broadens reach. Streamlining online sales processes enhances customer experience, driving higher engagement and increased revenue opportunities.
-
Cost management
The manufacturing sector faces rising financial pressures, from soaring material costs to supply chain disruptions. Ensuring supplier quality while managing cash flow and cutting expenses is vital. Centralized data, optimized warehouse management, and advanced analytics improve efficiency, ensuring better financial oversight and stronger operational performance.
-
Improved operational efficiency
Automation boosts manufacturing capabilities by simplifying repetitive tasks like data analysis, freeing time for high-value projects. Automated billing systems expedite revenue tracking, reduce audit expenses, and improve financial accuracy. These solutions help businesses adapt to evolving revenue standards while ensuring compliance and performance.
-
Precision and reliability
Cutting-edge technologies revolutionize product design and development by enabling real-time monitoring of equipment and processes through predictive maintenance and digital twins. These innovations uphold production quality while reducing downtime. Additionally, automation and 3D printing foster precision and uniformity, ensuring more reliable and efficient manufacturing outcomes.
-
Versatility and responsiveness
Manufacturing technologies empower industries to adapt swiftly to market shifts. Real-time data refines operations, meeting customer demands efficiently. Advanced financial solutions consolidate data, ensuring adherence to global regulations. Customizable cash flow forecasting improves accuracy, facilitating real-time insights, trend analysis, and predictive invoicing for better decision-making.
-
Lowered costs
Using digital tools allows businesses to gain deeper visibility into logistics network challenges, including stock levels, shipment progress, and demand fluctuations. This transparency minimizes risks and lowers costs by preventing surplus inventory. Such benefits initiate smoother operations and enhance overall supply chain efficiency for sustained business growth.
-
Sustainability
Digital advancements play a key role in sustainable manufacturing. These also improve energy efficiency by tracking and optimizing consumption across processes, including product testing. Better quality control helps reduce waste, ensuring more sustainable production methods. These innovations support net-zero goals while maintaining high manufacturing standards.
(Also read: The Future of China’s Industrial Strength)
Adoption challenges
However, manufacturers face challenges in keeping up with rapidly evolving digital advancements because of these factors.
-
Considerable upfront costs
High initial expenses can make digital transformation challenging for manufacturers. Adopting advanced technologies demands substantial investment, which can be a barrier for companies looking to modernize their operations.
-
Mindset shift
Manufacturers have long focused on hands-on production, making the transition to digital solutions difficult. Adapting to new technologies requires a shift in mindset and processes, which can be challenging.
-
Fear of disruption
Integrating digital technologies can temporarily halt operations, leading to lost productivity and revenue. Adapting to new systems also requires training, restructuring, and overcoming uncertainty about long-term benefits.
-
Struggles with tech integration
Manufacturers struggle to select the right digital tools as technology rapidly evolves. The risk of investments becoming obsolete, coupled with integration complexities and the need to upskill employees, contributes to hesitation in adopting digital transformation.
-
Lack of digital expertise
Many manufacturers face challenges in adopting digital tools due to gaps in technology knowledge. Workers and decision-makers may oppose adopting new technologies, favoring established methods they are comfortable with. Without clear guidance, companies risk falling behind competitors that successfully integrate advanced digital solutions into their manufacturing processes.
Strategies for embracing digital transformation
Despite obstacles, these strategies help manufacturers break out of their comfort zones and achieve greater success.
-
Implement in stages.
The high initial costs of digital transformation can be overwhelming, but viewing it as a long-term investment brings efficiency and savings. Starting small with pilot projects helps refine strategies before scaling. Seamless integration is key. Begin by selecting flexible, scalable solutions compatible with existing systems, reducing complexity and improving your chances for success.
-
Bring everyone on board.
Resistance to change is common, especially in traditional manufacturing. Conveying the advantages of digital transformation helps gain stakeholder support. Providing guidance and resources makes adoption smoother. Engaging employees at every level fosters collaboration, allowing their input to address challenges and refine strategies for a more effective transition to digital solutions.
-
Invest in upskilling.
A shortage of digital skills can obstruct the adoption of new technologies. To overcome this, investing in ongoing training programs is crucial. Equipping your team with the necessary digital knowledge ensures they can confidently manage and utilize new tools, facilitating smoother integration and improving overall effectiveness in the digital transformation process.
-
Safeguard sensitive data.
As manufacturers embrace digital solutions, protecting sensitive data becomes increasingly vital. Strengthening cybersecurity protocols and adhering to regulatory standards help safeguard information from breaches. Prioritizing secure systems and proactive risk management ensures digital advancements are implemented safely, minimizing vulnerabilities and reinforcing trust in technology-driven manufacturing processes.
-
Focus on continuous growth.
Digital transformation is a continuous process that requires ongoing evaluation. Regularly reviewing progress helps identify gaps, while gathering feedback ensures strategies remain effective. Making necessary improvements allows businesses to stay competitive, adapt to technological advancements, and meet changing market demands, securing sustained growth in an increasingly digital manufacturing landscape.
Adopting digital transformation is a strategic move that enhances efficiency, reduces costs, and strengthens market position. While challenges exist, the long-term benefits—greater agility, improved decision-making, and enhanced product quality—far outweigh the risks. Manufacturers that invest in digitalization today will be better positioned for future growth and industry advancements.As one of the Top 20 EMS companies in the world, IMI has over 40 years of experience in providing electronics manufacturing and technology solutions.
We are ready to support your business on a global scale.
Our proven technical expertise, worldwide reach, and vast experience in high-growth and emerging markets make us the ideal global manufacturing solutions partner.
Let's work together to build our future today.
Other Blog
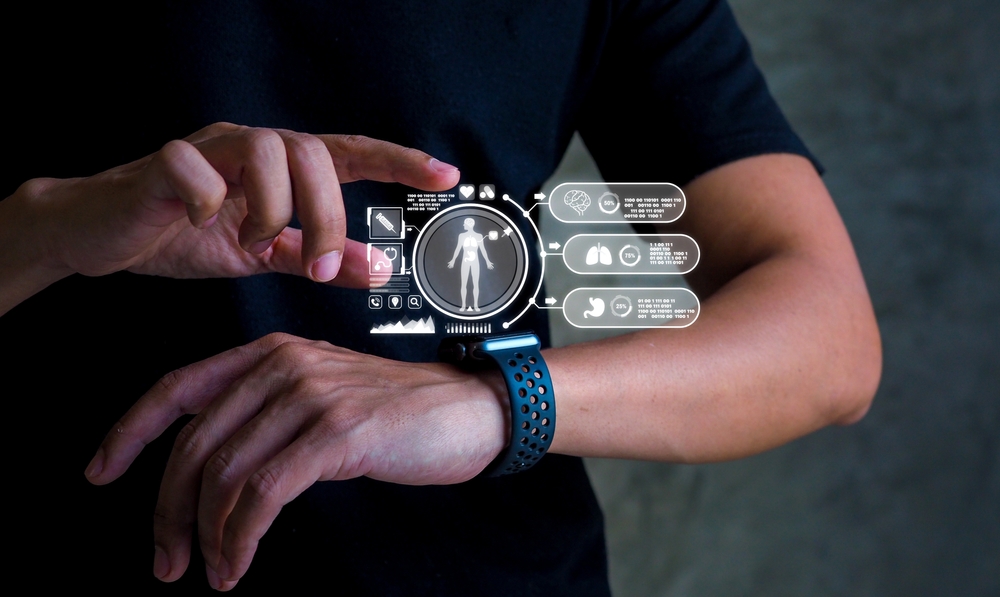
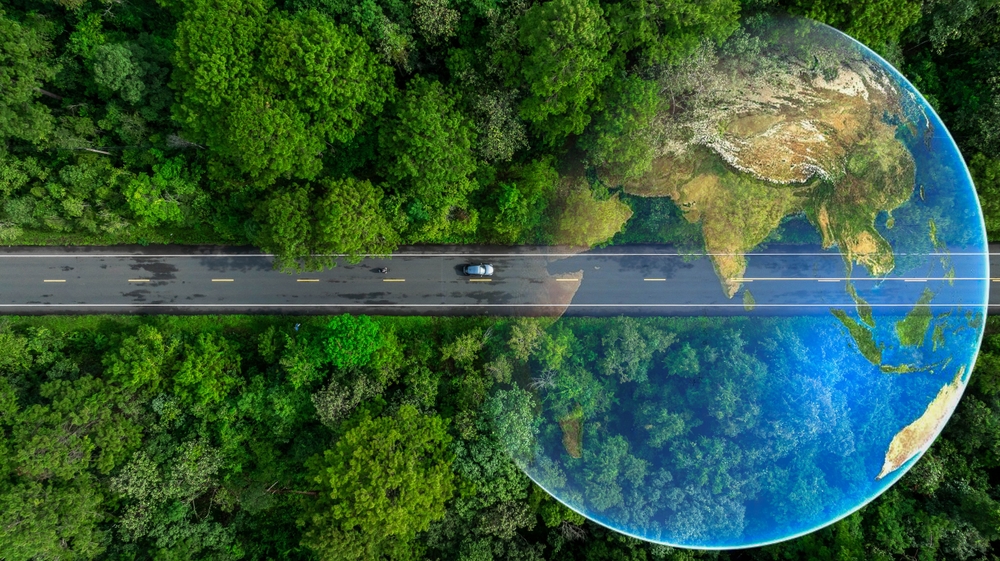
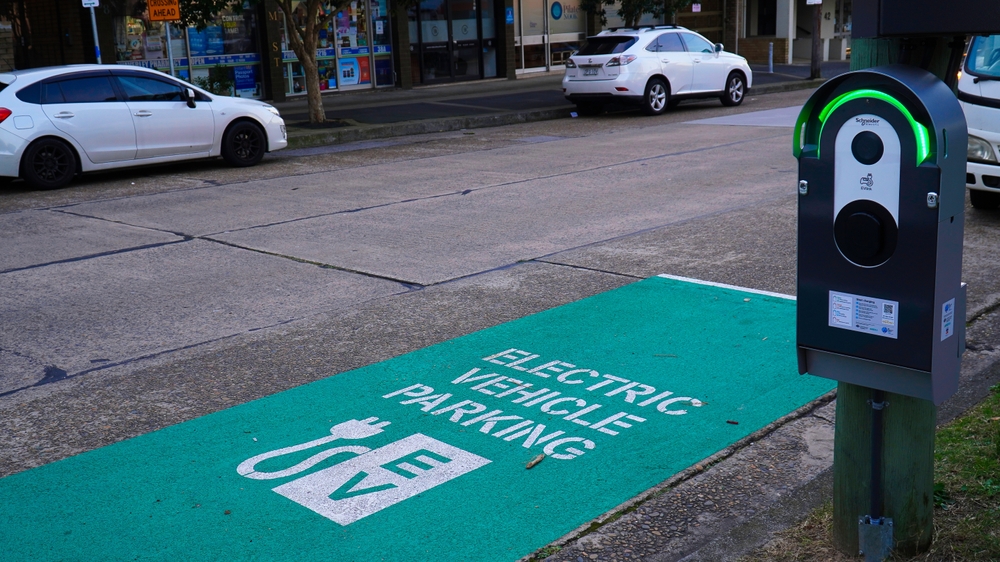