Connect With Us
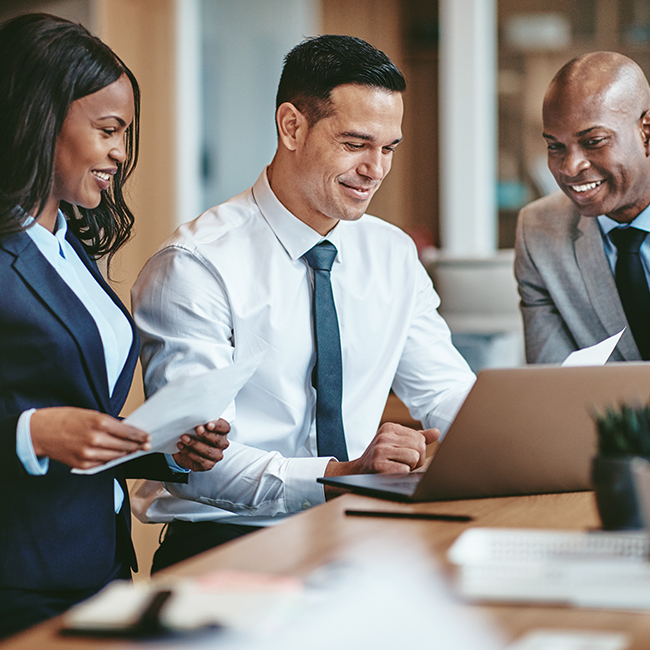
The article below appears on SMT Magazine online:
http://iconnect007.uberflip.com/i/373246
For years, the production line back ends at most EMS companies have been primarily manual. While board assembly technology has undergone many improvements in terms of equipment automation, from faster pick-and place machines and smarter reflow ovens to 3D inspection and flying probers, the back-end operations for final assembly and testing have remained largely non-automated.
Many reasons have been proposed to explain this reticence, including the high up-front cost of automation, a lack of standards, the wide variety of components and processes required, and decreasing product life cycles. There are, however, numerous reasons for EMS providers to look more closely at automating their back-end production lines—if not completely, at least partially. Not only are labor costs rising worldwide but quality requirements are getting more stringent as well. OEM customers continue to demand single-digit DPPM (defective parts per million) and continuous cost reduction programs.
Adding Value with Automation
In the end, the value of automation boils down to decreasing costs and increasing revenue. Let us look a little closer at both, starting with costs. If implemented judiciously, automation will increase throughput, improve quality, increase repeatability, and reduce labor-related costs.
The traditional reason that manufacturing engineers have long offered when attempting to justify automation has been the reduction in the number of manual operators. But this is no longer sufficient. Not only is it unfair to the project proponent, since the project might actually be more attractive than he is able to present it, but it is also unfair to the company, since it cannot reap the benefits of an automation project that is wrongly pushed aside.
At Integrated Micro-Electronics, we developed a financial tool for evaluating the return on investment on proposed improvement projects such as the automation of an assembly station, taking into account also the reduction in cost of non-quality due to factors such as yield improvements, lower inspection costs, lower rework costs, and fewer field returns. One challenge with such a tool is often the availability of reliable data from the departments involved, but we continue to improve the tool as we use it.
Reducing Total Manufacturing Cost with Automation
One example of a partially automated production line is a rotary assembly machine we developed and deployed at our factory in Jiaxing, China (Figure 1). It combines eight different production steps into a single, compact footprint. It checks the sub-assemblies after loading, performs the final assembly, does an optical test and a functional test, laser marks the finished assembly, checks the marking, and identifies and sorts bad parts from the good ones. Not only is there no manual handling of the parts during the entire final assembly sequence, but there is also an added high-resolution 3D inspection step.
We continuously evaluate the benefit of automation at our manufacturing facilities, including those in traditionally low-cost China. Automation strongly supports our zero-defect program in China by improving quality and repeatability at critical process steps where a high turnover of staff would otherwise have had a particularly debilitating effect. Typically, however, we continue to use manual operators for noncritical steps and for loading and unloading parts in and out of any automated equipment.
Looking now at the revenue side, automation will often enable a manufacturer to take on customer projects for which a demanding OEM or Tier 1 customer would otherwise not have considered them as a supplier due to the volume, the quality requirements or the complexity involved. For our high-volume quotations, investment alternatives with and without automation are compared as a matter of course. Automotive and medical-grade products likewise warrant close evaluation together with the customer, while complex products involving critical process steps such as precision press-fitting or selective soldering are also considered for automation.
One example of a technology-enabled production line is the plastic injection molding operations at our factory in Guadalajara, Mexico (Figure 2). We developed a dual-robot handler to automatically stamp pin inserts from a reel, insert the pins in multiple cavities in the injection molding machine with high accuracy, remove the finished parts, inspect them and finally sort them. Without automation, it would have been impossible to attain the tight tolerance in the insertion process, the high repeatability in the cycle time, and the high uptime of the injection machine. In addition, the unique system is designed with a minimum of mechanical hardware in order to decrease setup time, maximize reliability and minimize maintenance costs.
An additional source of revenue for an EMS provider could also be the automated equipment itself. The design, supply and support of customized assembly and test equipment could be a valuable revenue stream for any manufacturer. We have a group dedicated to the development of customized equipment, with teams present in all geographies in which we operate. Together with our design and development and advanced manufacturing engineering groups, we are able to provide a wide range of engineering services beyond just standard manufacturing.
The market for industrial automation equipment (IAE) is growing. It is set to grow 7% in 2014 to approximately US$185 billion from $173 billion in 2013, due in part to the recovery of global manufacturing, according to IHS. I am excited to note that the use of industrial robots in electronics manufacturing is on the rise.
Traditionally, there have existed two types of automation: 1) hard automation, with fast hardware-heavy machines optimized for the assembly of one type of product; and 2) flexible automation, with slower, reconfigurable cells designed to assemble a wider range of products. Robots are typically used in flexible automation.
Reducing Total Manufacturing Cost with Automation
One theory is that the increasing use of robots among EMS companies is due to the decreasing costs and increasing functionality of industrial robots. Robot manufacturers appear to be recognizing that the limited space available on a typical electronics production line, especially at a low-cost location, limits the selection of robots that can cost-effectively be used. Some of the newer robots such as the FANUC M-1iA are designed to be relatively easily integrated side-by-side with human assembly operators.
Even more exciting is the coming wave of collaborative robots, which can operate within the same workspace as human operators without any safety fence. Collaborative robots are available now from manufacturers such as KUKA, Universal Robots, and Yaskawa Motoman. One impressive at the recent Automatica Trade Fair for Automation and Mechatronics in Münich showcased an upcoming dual-arm collaborative robot from ABB with 14 axes, flexible grippers and camera-based part location, specifically designed for small-part assembly operations common in the electronics industry.
At the same trade fair, the European Commission and the euRobotics umbrella organization launched the world’s largest civilian R&D program in robotics, with a total investment of €2.8 billion.
Automation may not be a panacea to an electronics manufacturer’s dilemmas, but is a valuable tool in any manufacturing engineer’s tool chest, and a valuable weapon in the fight against rising costs and shrinking profit margins
IMI will always be relevant, if not on the leading edge of the next big thing.