Challenges and Changes for Global Supply Chains
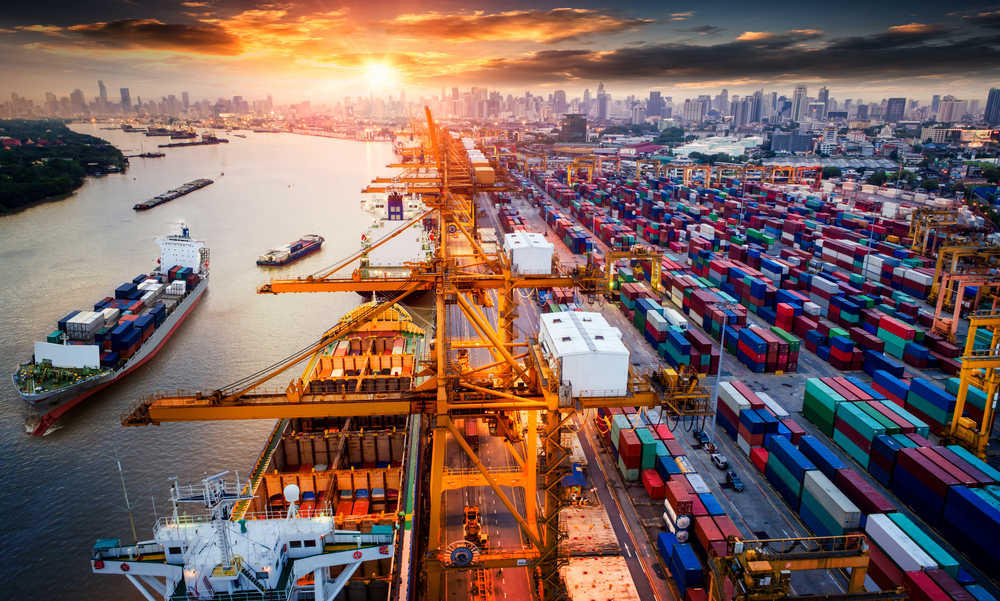
The COVID-19 pandemic put in stark relief the vulnerabilities of global supply chains. What challenges will the electronics industry continue to face, and what strategies are needed to weather future storms?
Over the past two years, the weaknesses in our global supply chains have been laid bare, aggravated by a pandemic, climate-related disasters, material shortages, and fluctuation demands. An agile, resilient, and visible supply chain is crucial to a company's survival and success--and this is especially true for the electronics industry, which continues to fight an uphill battle on many fronts.
In this article, learn what hurdles the electronics industry will have to overcome and what strategic changes to consider to thrive in the new normal.
High demand, constrained supply
From smart home appliances and remote work technology to telehealth and electric vehicles, semiconductors are woven into the fabric of our personal and business lives. Driven by digital transformation, the demand for semiconductors has surged during a time of material shortages and supply chain disruptions.
And these supply chain woes aren’t going away any time soon. Glen O’Donnell, Vice President and Research Director at Forrester, believes that demand will stay high while supply remains constrained and expects the shortage to last until 2023.
(Also read: Chip Shortage Puts the Auto Industry on Edge)
Geographic specializations, geopolitical tensions
Our world is becoming increasingly dependent on electronics, and our electronics supply depends on a small part of the world. Taiwan manufactures 92% of the world’s semiconductors under 10 nanometers. The Democratic Republic of Congo mines 60% of the world’s cobalt, which is considered the highest material supply chain risk in EV lithium-ion batteries.
A semiconductor product could pass through international borders 70 or more times before reaching the end customer. The supply of critical materials could easily be upended by trade wars, armed conflicts, and civil unrest.
Climate change, catastrophic events
From floods and heatwaves to hurricanes and winter storms, climate change is wreaking havoc globally. These extreme weather events are happening more frequently, taking lives, damaging infrastructure, and disrupting supply chains. An extreme weather event in the other corner of the world can destroy facilities, halt production, raise costs and prices, and lead to devastating profit losses.
According to the McKinsey Global Institute, the likelihood of a hurricane disrupting semiconductor supply chains may grow two to four times by 2040. These disruptions, which could last several months, could cost semiconductor suppliers up to 200% of their annual profit.
(Also read: Climate Technology: Time for a Cool Change)
Increasing digitalization, global e-waste
Electronics are now the fastest-growing global waste stream. Last year’s e-waste is estimated to total 57.4 million tons–outweighing the Great Wall of China, the world’s heaviest man-made structure.
The number of household electronics continues to grow: smartphones, laptops, smartwatches, monitors, VR headsets, television sets, gaming consoles, and other appliances that are essential to our digital lifestyles. And we’re discarding them at a faster rate, whether it’s because of breakdown, wear and tear, or a newer model hitting the market.
Containing hazardous materials such as mercury, lead, and cadmium, e-waste poses a threat to human health and the planet. It is a global environmental issue that must be addressed.
(Also read: Why Your Gadgets Are Built to Fail)
Risk-aware, not risk blind
As supply chain risks continue mounting, companies must identify the inherent vulnerabilities in their supply chain and their level of exposure to unforeseen shocks.
Supply-chain vulnerabilities occur in five areas, according to McKinsey:
- planning and supplier networks
- transportation and logistics systems
- financial resiliency
- product complexity
- organizational maturity
Exposure can come from four main sources:
- force-majeure shocks (natural disasters)
- macropolitical (economic shocks)
- malicious actors (cyberattacks)
- counterparties (fragile suppliers)
“The most advanced businesses will model the size and impact of various shock scenarios to determine the actions they should take to rebuild their supply chains and mitigate future risks,” says McKinsey.
To withstand shocks or disruptions in their global supply chains, companies should balance their onshore, nearshore, and offshore strategies. Identifying alternate sourcing strategies and a broader vendor list can improve access to supply and help alleviate allocation issues.
A digitally-enhanced supply chain for increased visibility
“If you can’t measure it, you can’t manage it,” management guru Peter Drucker famously said. To become more resilient to supply chain disruptions, deep visibility and comprehensive information beyond their Tier 1 suppliers is key.
By collecting, consolidating, and consuming real-time data and insights from across the supply chain, companies can be alerted to possible supply chain issues before they emerge and respond accordingly. By communicating and collaborating closely with partners, suppliers, and customers, everyone involved in the supply chain will be armed with information to help plan more effectively.
With data and software analytics, companies will have end-to-end supply chain visibility, allowing them to use predictive analytics to make more informed, real-time decisions, increase production agility, and leverage automated processes.
(Also read: How to Protect Yourself from the Rise of Ransomware)
A balance between just-in-time and just-in-case
Developed by Toyota engineer Taiichi Ohno in the 1950s, just-in-time production reduces inventory across the supply chain, helping companies increase production efficiency while decreasing waste and increasing profits.
“These practices were subsequently embraced by innumerable industries to achieve the same economic benefits,” writes GaN Systems CEO Jim Witham. “But the extent of pandemic-related shortages across vast ranges of goods now challenges whether these benefits are worth the tradeoff if the result is a significant lack of preparation for future disruption.”
For their higher-value customers, companies could move from a “just-in-time” to a “just-in-case” approach, says PwC. By buffering their stock inventory and identifying multiple supply options for these premium customers, they can still guarantee delivery during disruptions.
The past two years have underscored the fragility of supply chains in our interconnected global economy. Disruptions are inevitable, and we need to reshape global supply chains to withstand and recover from the next big shock.
As one of the Top 21 EMS companies in the world, IMI has over 40 years of experience in providing electronics manufacturing and technology solutions.
We are ready to support your business on a global scale.
Our proven technical expertise, worldwide reach, and vast experience in high-growth and emerging markets make us the ideal global manufacturing solutions partner.
Let's work together to build our future today.
Other Blog
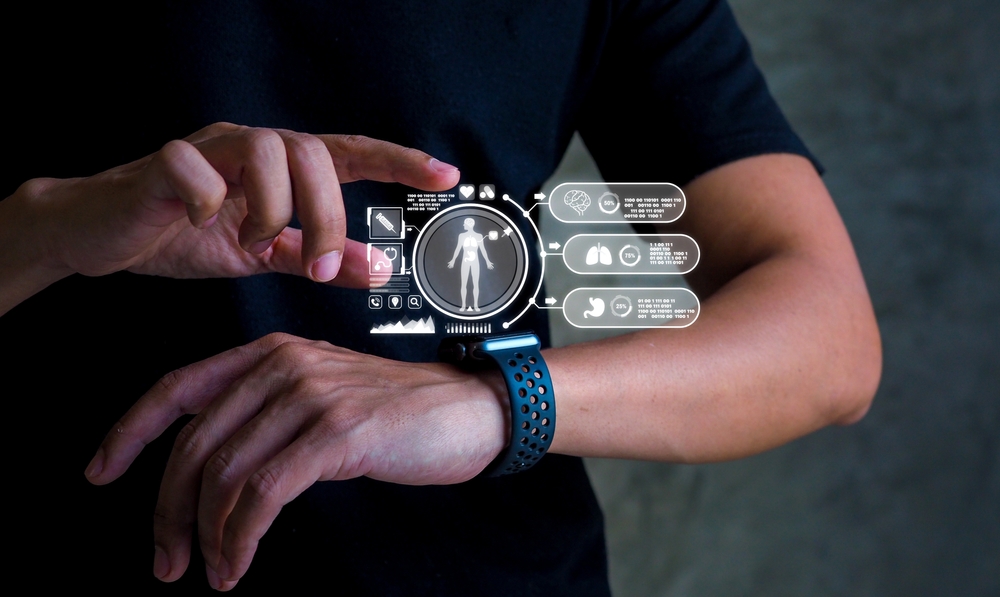
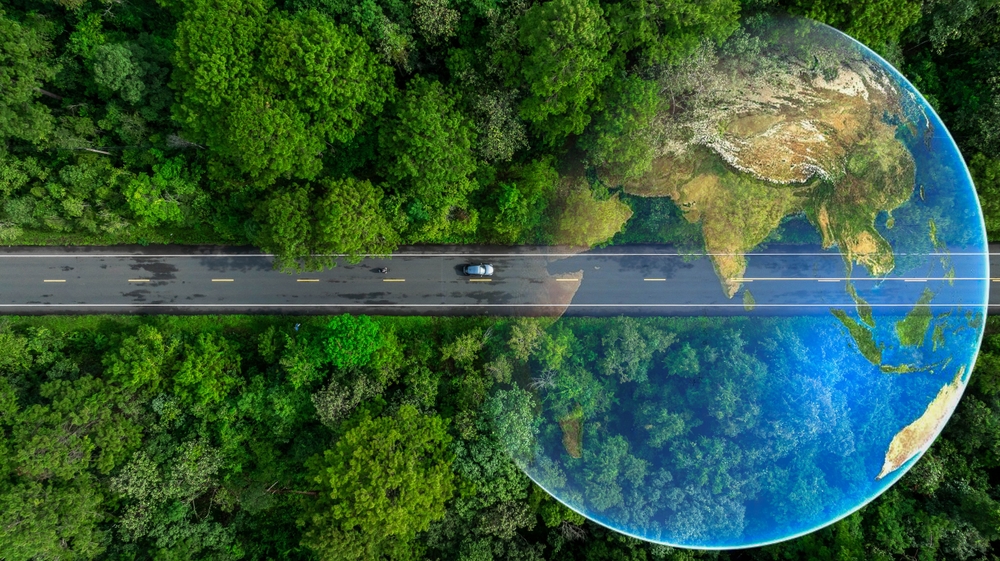
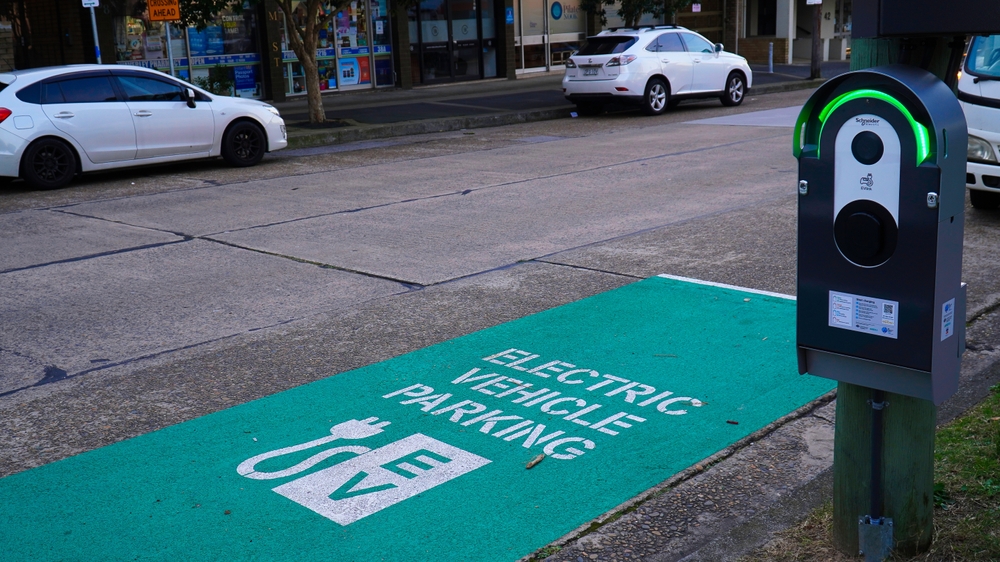