Shifting Gears to EV: OEM’s Next Challenge
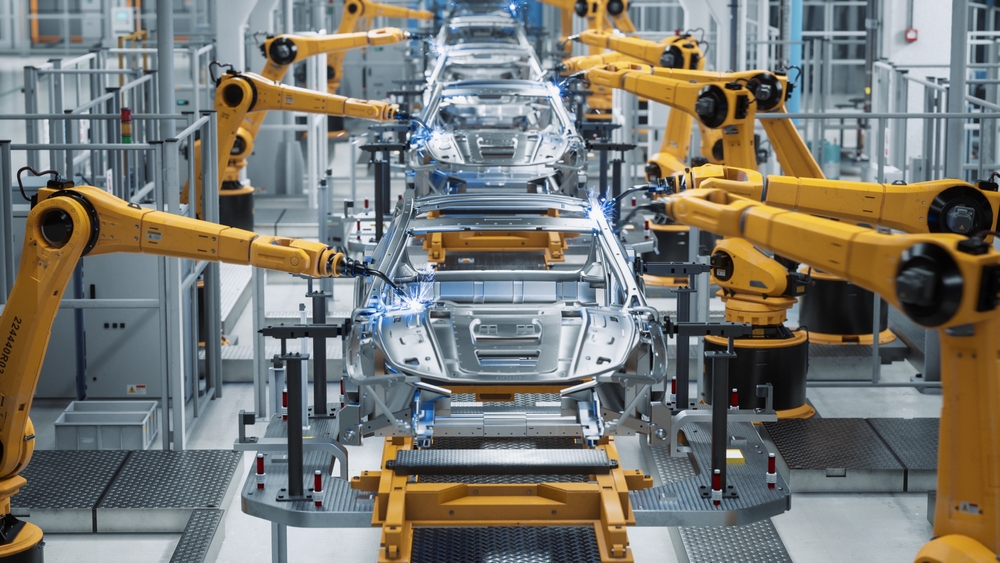
As we move steadily towards using more electronic vehicles, the growing demand for EVs puts the pressure squarely on the automotive industry. Here’s how carmakers can rise to meet this new challenge.
According to leading global industries information provider IHS, EVs comprise 3% of today’s automotive market. However, this figure is estimated to balloon up to 50% by 2026, and by 2029, it may even rise to 60%. This projection means a drastic shift in the kind of vehicles we drive in less than ten years. Can carmakers keep up with the accelerated demand for EVs?
A global manufacturing services company recently released a paper for the automotive industry recommending solutions for carmakers and OEMs. Beset with many challenges at the onset, including the microchip shortage, OEMs now face the new challenge of meeting the automotive sea-change when it comes to the demand for EVs.
(Also read: From Automakers to Chip Makers: Will DIY Save the OEMs?)
A supportive infrastructure for EVs
Many manufacturing service companies work hand-in-hand with OEMs in making cars that are ready for the market so it’s natural that these companies would want to offer solutions to help support the changing requirements that come with the production of EVs.
These companies urge OEMs to review existing business models and methodologies to accommodate the requirements of manufacturing EVs because making these is very different from making ICE (internal combustion engine) cars. In the simplest terms, EVs are a very different beast, and these require a different way of making from “normal cars”.
First, a supportive infrastructure must be established for EVs. Manufacturing service companies are a vital component of this infrastructure for the automotive industry, and their importance will increase along with the demand for EVs. An ecosystem that is based on solid partnerships between OEMs and their respective manufacturing service companies is needed, with a clear delineation of roles for each.
Workflows will need to be reviewed and adjusted to empower both the OEM and the manufacturing service company. The objective is to optimize the supply chain and minimize risk for both. More than ever, the OEM and manufacturing service company need to work hand-in-hand seamlessly to meet goals of driving down costs, ensure high quality during manufacturing, allow for precise testing, and speed up production for the anticipating market.
A different beast
Manufacturing services companies remind OEMs that there is a world of difference between ICE cars and EVs. EVs require an entirely separate factory for manufacture, not just a separate assembly line. The cost to build these factories is an important factor that has been noted, and it has become necessary for manufacturing service companies to point this out to OEMs.
What should OEMs do during this transition from ICE models to EVs? Manufacturing service companies recommend solutions to work around how OEMs can overcome challenges with investments and what to do with aging assets (i.e., ICE models that may not sell as well as these have in the past).
One solution is for OEMs to consider sharing investment and sales channels with another partner, even a competitor. A good example of this is Ford making use of Volkswagen’s EV platform. Conversely, Volkswagen has used Ford’s platform for pickup trucks.
How specialist suppliers help the supply chain
If the manufacture and production of EVs is a different beast, then so too would be predicting how its market will behave. Strategies for ICE models will no longer be applicable when it comes to moving EVs in the market, which poses yet another challenge to OEMs.
New components needed to build the EVs such as microprocessors, cables, and connectors are becoming more important. OEMs are urged to consider sourcing requirements for charging stations for EVs.
The importance of working and collaborating with multiple specialist suppliers is underscored. Some suppliers are responsible for handling processes, as well as having the proper equipment to manage the volume of orders. Other suppliers are tasked to handle installation, maintenance, and repair. OEMs need to identify these requirements and select which suppliers to work with. Multi-sourced and localized specialist suppliers are needed to reduce logistics costs.
A highly specialized process
The sweeping changes to the automotive industry can be attributed to the synthesis of traditional automotive manufacturing and electronics. It isn’t simply a matter of adding an electronic component to an automotive one. The process becomes highly specialized to an understanding of both fields to create something entirely new.
An investment towards in-house specialized skills, knowledge, training, and practice is required of OEMs. While the road to electrification may be a highly charged one, automotive industry professionals are optimistic that OEMs are shifting their strategies in favor of EVs. However, OEMs cannot do it alone. Leveraging their manufacturing services providers and being open to more empowering collaborations with specialist suppliers is the key to adapting, evolving, and moving forward.
As one of the Top 21 EMS companies in the world, IMI has over 40 years of experience in providing electronics manufacturing and technology solutions.
We are ready to support your business on a global scale.
Our proven technical expertise, worldwide reach, and vast experience in high-growth and emerging markets make us the ideal global manufacturing solutions partner.
Let's work together to build our future today.
Other Blog
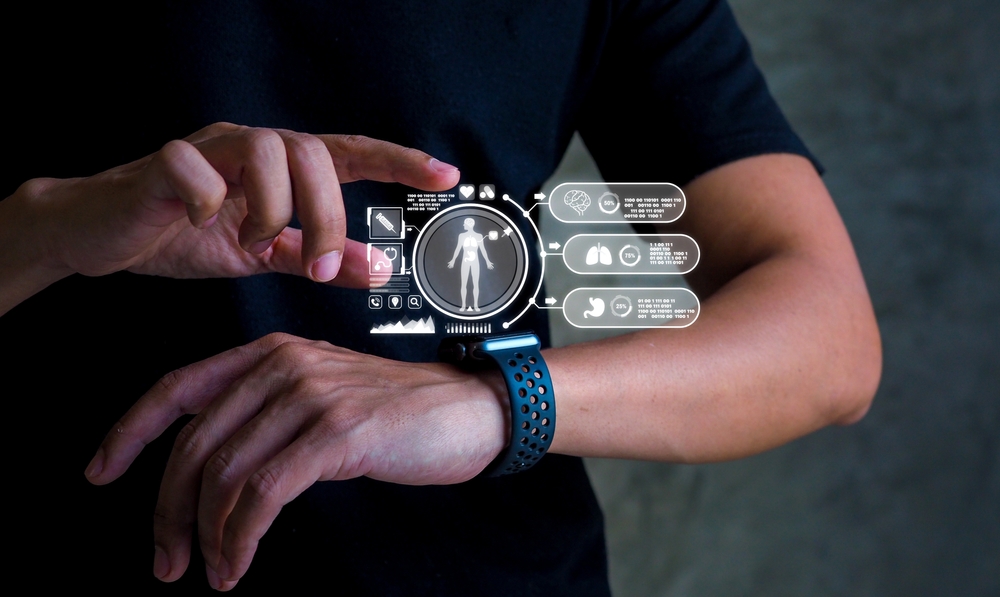
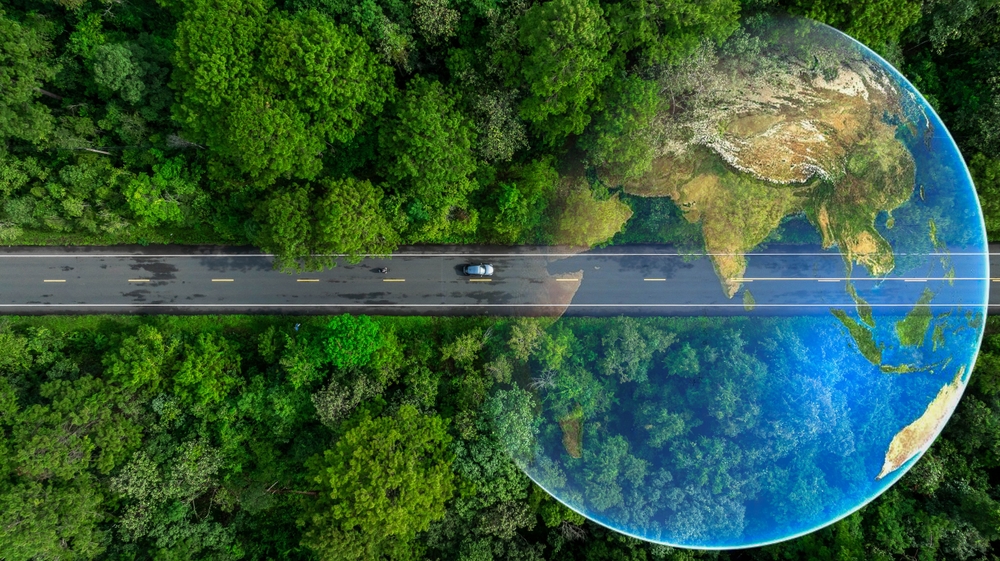
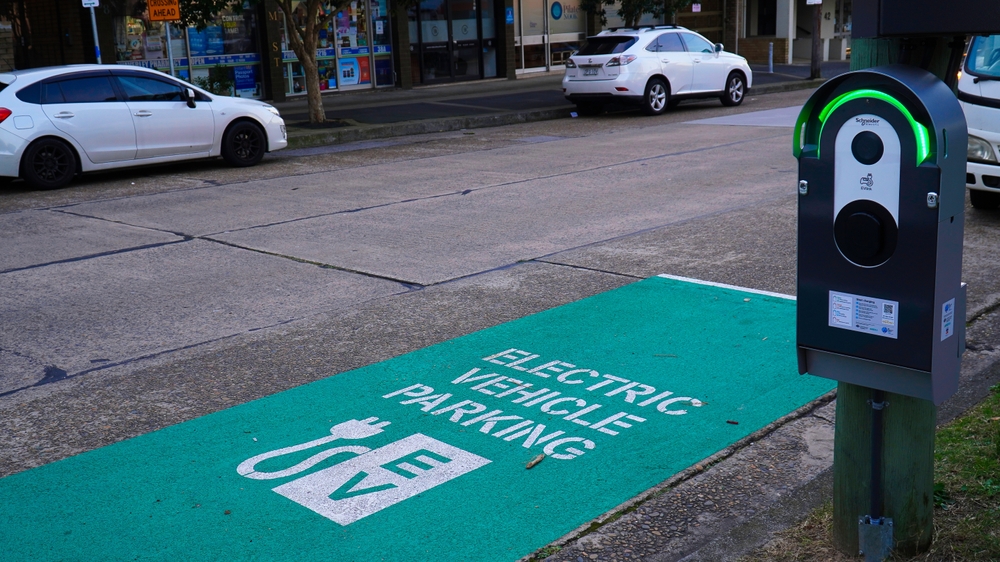