This Tech Took 200 Years to Make
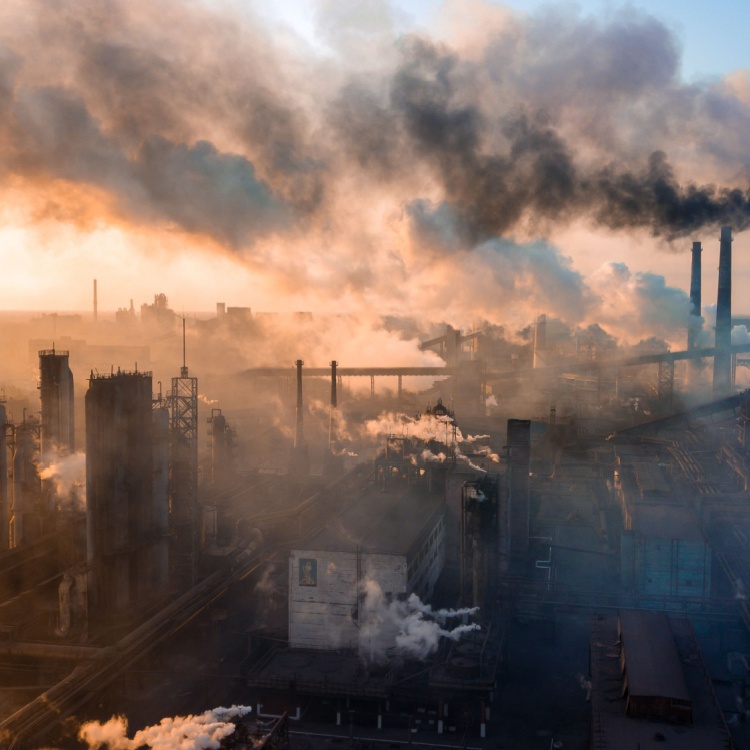
In 1824, French physicist and military engineer Nicolas Léonard Sadi Carnot designed a theoretical model for the most efficient heat engine possible. Known as the Carnot engine, it uses thermal analysis to define the maximum efficiency achievable when converting heat into work, forming the foundation of modern thermodynamics.
Today, London-based Carnot Engines is innovating engine technology for the renewable energy market. Founded in 2019 by three engineers, the company focuses on reducing carbon emissions in large-scale uses such as heavy-duty vehicles, maritime vessels, and power systems.
Leveraging a 200-year-old energy principle
A Carnot engine is like the perfect heat engine—designed to turn heat into useful work as efficiently as possible. Imagine it as a machine working between two “heat zones”: one very hot and one cooler. The hot zone provides energy, and the cooler zone helps eliminate leftover heat. Here's how it works step by step:
-
Absorbing heat
First, the engine takes in heat from the hot zone and uses it to expand a gas. This expansion makes the gas push against something, like a piston, creating motion (mechanical work). A pressure gauge is used to monitor the gas pressure during this process.
-
Cooling off while working
Next, the gas keeps expanding but doesn’t take in more heat. It cools down as it continues to do work.
-
Releasing heat
Then, the engine compresses the gas, forcing it to release heat into the cooler zone.
-
Resetting the cycle
Finally, the gas is compressed further without losing heat, getting it back to its starting temperature so the cycle can begin again.
This cycle repeats over and over.
Sadi Carnot, the inventor of this idea, showed that this process sets the highest efficiency any engine can achieve—meaning no engine can do better than this at turning heat into work.
However, real engines can't reach this perfection because of friction, heat loss, and material limits.
By leveraging innovations in materials, design, and engineering, Carnot Engines has developed a heat engine capable of achieving 70% of Carnot’s theoretical efficiency—nearly double that of traditional engines. This breakthrough stems from a unique architecture that supports higher temperature differences. When operating on hydrogen, it produces zero emissions, with water vapor as the only by-product.
Over the past five years, the company has fine-tuned its technology to ensure it meets practical demands. Carnot Engines has successfully demonstrated that an engine inspired by Carnot’s principles can handle the challenging conditions required for modern applications.
Fuel flexibility
Carnot Engines combines system integration with advanced engineering capabilities to create a highly efficient, fuel-flexible heat engine. Its adaptable design allows operators to switch between hydrogen, ammonia, methanol, biofuels, and conventional fuels, optimizing cost and emissions as energy markets evolve.
This flexibility is crucial for hard-to-decarbonize sectors like shipping and other heavy industries, enabling a smoother transition to cleaner energy.
By offering both increased operational efficiency and a versatile fuel strategy, the company provides a practical pathway toward reducing emissions, with the potential for true zero-emission operation when using hydrogen or other clean fuels.
Carnot’s advancements in testing solutions have attracted strong interest from investors and the U.K. government. The company has secured millions in government grants, including a £1.5-million Energy Catalyst Grant and funding through the U.K.’s Department for Transport’s Clean Maritime Demonstration Competition.
Recognizing Carnot’s potential, Japanese shipping giant Mitsui O.S.K. Lines (MOL) has invested in the company, becoming a key partner in the maritime sector. Together, they are developing a Maritime Auxiliary Power Unit (APU) designed for MOL’s fleet. This collaboration leverages Carnot’s high-efficiency engine technology to lower fuel consumption and emissions while maintaining fuel versatility.
Carnot has recently partnered with Compact Syngas Solutions to supply 200 kilograms of hydrogen for a 40-day sea trial of its zero-emission marine engine. Before deployment, the engine will undergo testing at Brunel University. The trial, set for March 2025, will take place aboard a Carisbrooke Shipping K-class cargo vessel, operating between Bristol and Belfast.
Arduous process
Developing Carnot’s high-efficiency engine required overcoming significant technical challenges. By utilizing advanced ceramics and cutting-edge industrial manufacturing techniques, engineers addressed material limitations that previously prevented engines from handling extreme temperature gradients and pressures. Thoughtful design methods have enabled the engine to operate efficiently where traditional materials would fail.
New manufacturing solutions like 3D printing enable the production of custom parts on demand, while precision machining techniques ensure micro-scale accuracy, reducing energy losses and enhancing overall efficiency. Carnot’s engines use sensors and onboard intelligence to optimize performance in real time.
However, as the company scales, the global manufacturing sector faces a persistent skills gap. Finding experts in ceramics, advanced manufacturing, and power electronics remains a challenge amid ongoing talent shortages.
To fill the gap, Carnot has focused on apprenticeships, recruiting young talent straight from college. Apprentices spend one day a week in school and four days gaining hands-on experience in the workshop, allowing the company to develop the necessary skills over time.
Although it takes years to fully develop these apprentices, the company sees it as an effective strategy. The recruits are eager to work with their hands and engage with engines and tools, and by fostering an exciting environment, Carnot has been able to retain them.
For its senior roles, the company capitalized on its connections with the Formula 1 industry. Through these, Carnot has successfully recruited seasoned professionals with 20 to 30 years of experience, many seeking new challenges or a better work-life balance.
What made Carnot successful?
Carnot’s technology stands out because previous attempts to create efficient heat engines, like adiabatic engines in the 1970s and 80s, failed due to issues with materials and established manufacturing practices. Ceramics, though excellent in high temperatures, couldn’t handle the stress of engine movements.
Additionally, original equipment manufacturers (OEMs) faced challenges adapting their existing infrastructure and designs, often using coatings that caused material expansion issues. Developing a new engine type requires a fresh approach, not just adaptations of old designs.
As one of the Top 20 EMS companies in the world, IMI has over 40 years of experience in providing electronics manufacturing and technology solutions.
We are ready to support your business on a global scale.
Our proven technical expertise, worldwide reach, and vast experience in high-growth and emerging markets make us the ideal global manufacturing solutions partner.
Let's work together to build our future today.
Other Blog
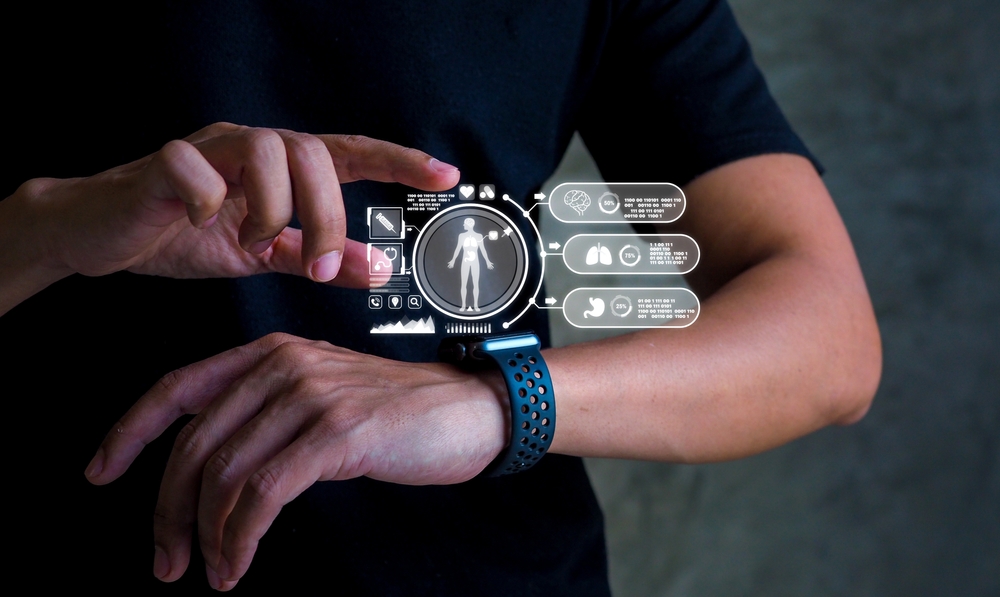
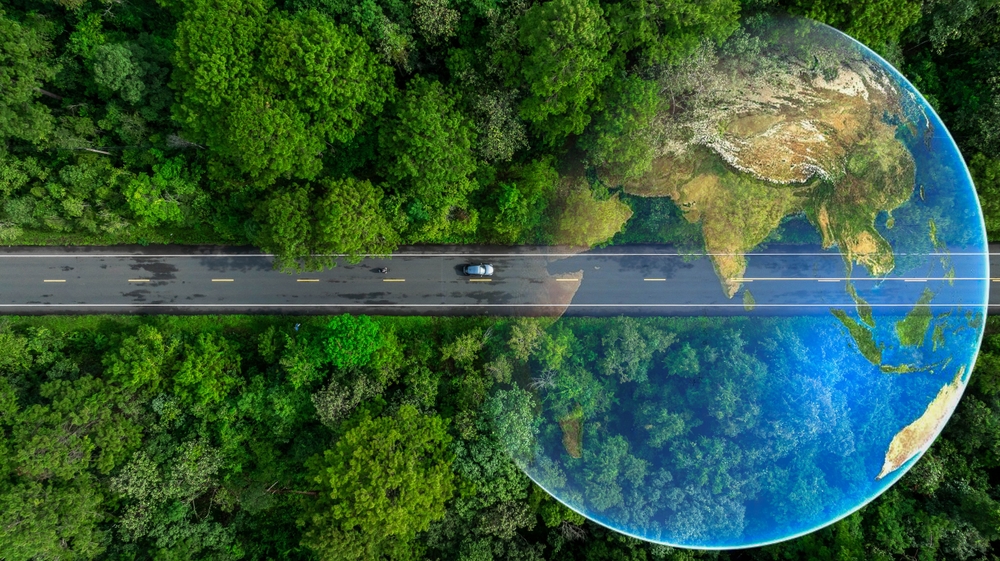
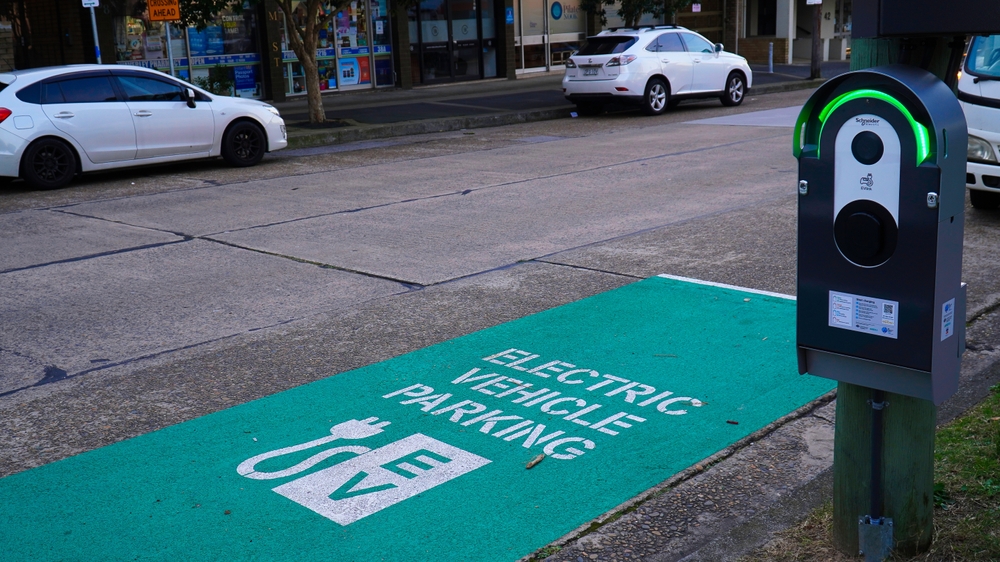