How EV Batteries Are Tested
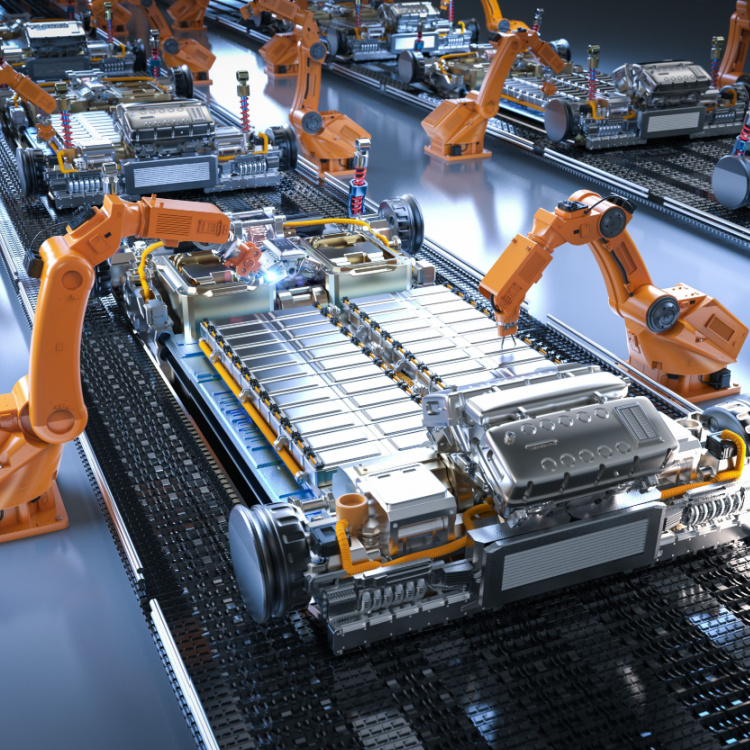
Electric vehicles (EVs) are gaining global acceptance, but their long-term success largely depends on their batteries' qualities and capabilities. EV batteries must be stringently tested for safety and dependability, especially with their growing adoption and popularity.
With environmental issues worsening, the Paris Climate Agreement calls on partner countries to strengthen their commitment to reduce global emissions to zero in the latter part of the century and limit temperature rise to below 2°C.
Research has shown that the transportation and power sectors account for almost 60% of the world's carbon emissions. To this percentage, passenger vehicles are the main culprit, contributing 60%, while medium to heavy-duty trucks make up 23%. With these findings, the logical step is to transition from petrol-powered cars to EVs. Thankfully, the public seems receptive to the idea, as shown by the growth of the EV market.
The importance of EV batteries
As one of the most essential components of EVs, batteries need to be developed and tested to meet EV manufacturers' standards and requirements. Batteries are also crucial in lowering EV relatively high prices, which prevents the market from fully flourishing.
Currently, the Lithium-ion EV battery is the most preferred and widely accepted by EV companies because of its clear advantages, including affordability, power density, and safety. There are many kinds of Lithium-ion batteries, and one that's been making waves is the Lithium iron phosphate (LFP) battery. Tesla, Ford, Volkswagen and Toyota Motor are only some of the established automakers that have embraced LFP technology. This positive response is compatible with Fortune Business Insights' prediction that the LFP market will grow by 25% by 2028.
How are EV companies strategizing to find batteries that suit their needs? Some collaborate with battery producers, while others construct dedicated battery production plants to create batteries for their future EVs.
Also read: The Chip Crunch: How It Affects Automakers
Why conduct EV battery testing
Battery failure poses considerable risk for users and people around them. This is why strict safety guidelines are set for EV battery production. Government regulations, international best practices, customer needs and internal standards contribute to safety-based recommendations. Here are some reasons why EV battery testing is a must.
- Complex systems
Batteries store elevated amounts of electrical energy and utilize sophisticated electrical systems. Aside from the battery pack, its internal components and interactions are tested to ensure safety, compatibility and quality. According to this university study in Finland, testing should be qualitative and quantitative—the latter can be measured scientifically, such as in energy density and voltage. Meanwhile, qualitative assessments often involve simpler tests that involve the senses like sight, touch and smell, evaluating properties such as battery size and temperature.
- Daily usage
Because customers are likely to use their EVs regularly, batteries should be able to withstand the rigors of daily driving. While developing battery management systems, engineers test them in real-world environments to verify efficiency and confirm standard compliance. Battery analysis involves replicating tangible inputs and extraneous digital connections to the unit while observing its reactions and performance in relation to the specified design criteria. Ultimately, the only effective method to ensure your battery's safety and reliability is by simulating the changes in temperature, cell voltages and other components it may encounter.
- Environmental stress
While EV batteries seek to lessen the transport system's environmental impact, environmental stress such as thermal shock, humidity, and charge-discharge cycles can also take its toll on them. Through the live monitoring of this series of performance tests conducted before and after stress implementation, manufacturers gauge quality control, develop troubleshooting techniques, and gain data for research and development.
- Customer safety and satisfaction
Through testing, manufacturers can pinpoint possible safety issues, like short circuits and thermal runaway, which can lead to accidents and fires. This process also checks if the battery meets expectations in range and power in different conditions. When batteries are certified safe, this builds customer confidence, encouraging more to use EVs. Testing also provides data on how batteries degrade over time and how to improve their longevity.
Kinds of battery tests
Formulating a test technique for something as complex and robust as an EV battery pack can get overwhelming. However, the method can be broken down into doable segments. It also helps engineers constantly develop testing software that produces faster and more accurate results.
The end goal of testing is to guarantee that the battery conforms to the highest standards of quality and dependability set by the Original Equipment Manufacturer (OEM). Procedures are customized to target specific requirements and appraise the battery's health. Here are some tests conducted:
- Vibration tests
Mechanical vibrations are inevitable during driving, so battery packs have to withstand these while maintaining optimum performance. These tests subject the battery to different vibration frequencies, durations and directions to see how well it can tolerate various conditions. All the while, testers take note of changes in current flow, voltage and temperature to see how vibrations affect the battery's performance and resilience.
- Thermal shock and cycling
EVs go through different weather conditions and terrains, which affect their temperature. With thermal cycling, testers see how batteries respond to temperature fluctuations in real-life situations. With these findings, researchers and manufacturers can optimize management systems, design safety mechanisms and potentially boost the battery's lifespan.
- Mechanical integrity
Mechanical issues in batteries, such as loose parts, structural defects and warping, can significantly impact the safety of EVs. Vehicles often cross uneven roads and mechanical stress; the battery must be structurally sound to endure these. With this testing, manufacturers can validate the battery's competence, reducing the risk of failures and accidents.
- Overcharge/discharge protection test
Batteries are infamous for their fast degradation due to excessive charging and discharging. Harmful situations such as thermal runaway, fires and rapid deterioration are avoided by ensuring that the battery's protection systems are in place and fully functioning. When batteries last longer, customers are safer and enjoy reduced maintenance costs.
Other necessary EV battery tests
- Fire resistance
- Thermal protection
- Water resistance
- External/internal short circuit protection
As one of the Top 20 EMS companies in the world, IMI has over 40 years of experience in providing electronics manufacturing and technology solutions.
We are ready to support your business on a global scale.
Our proven technical expertise, worldwide reach, and vast experience in high-growth and emerging markets make us the ideal global manufacturing solutions partner.
Let's work together to build our future today
Other Blog
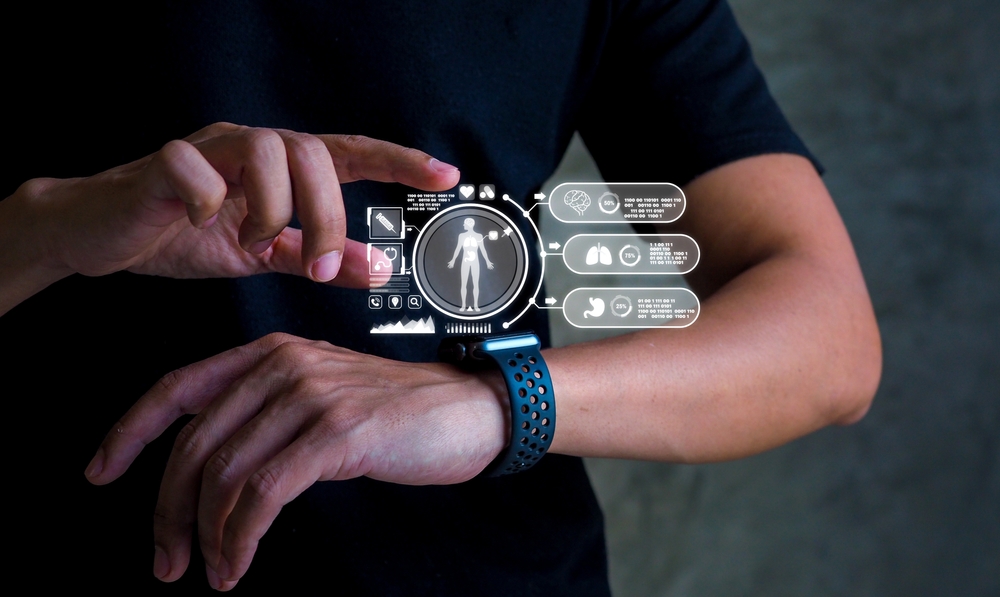
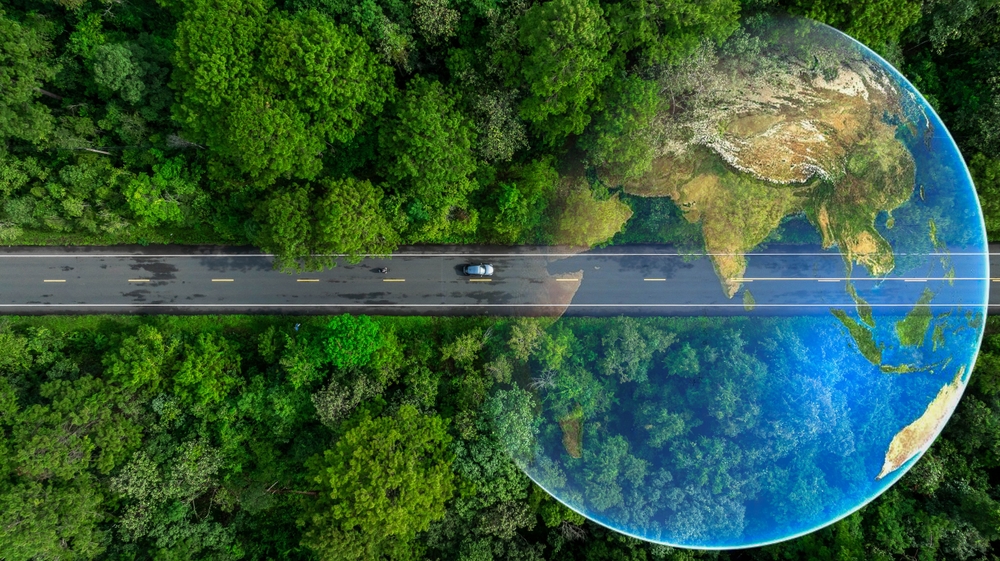
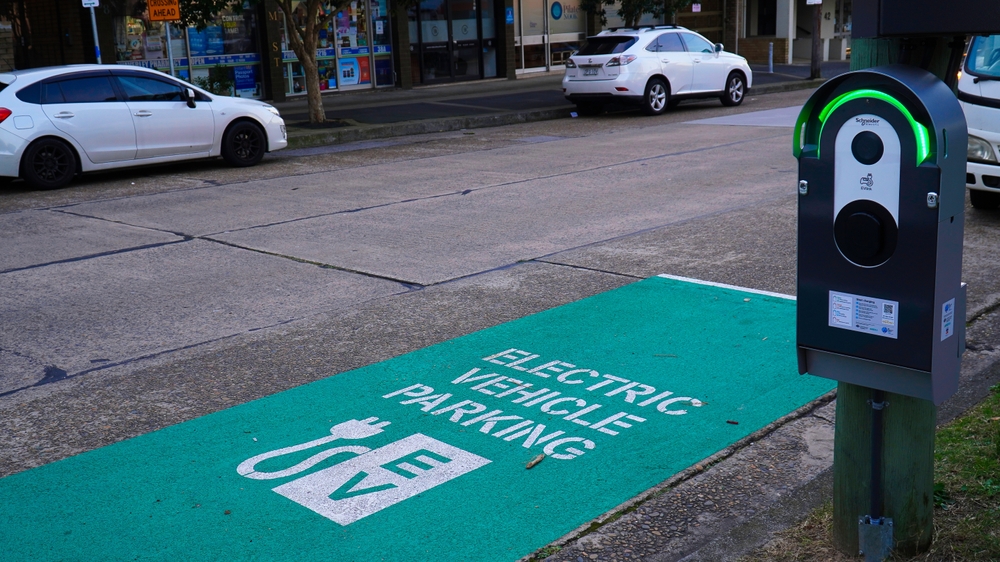