The Importance of Testing Materials
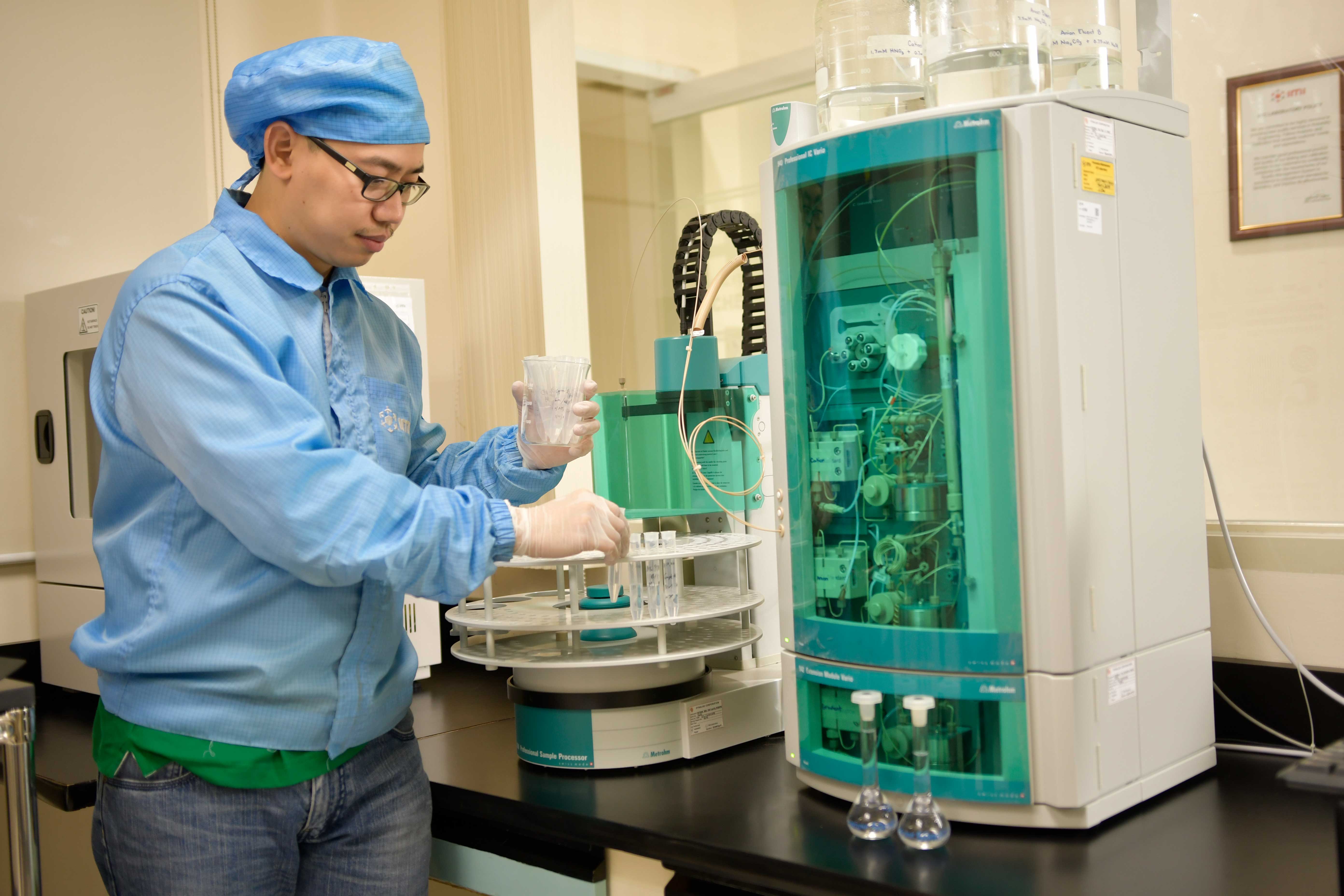
September 5, 2019 Philippines - From human hair to steel, almost any material can be tested, and it is highly important to do so in global manufacturing given the ever-fierce competition within the industry due to several factors like the advancement of technology and evolution of consumer demands.
In analytical testing and calibration, both the physical and mechanical properties of materials, prototypes, and samples to be used for production are being assessed to help manufacturers come up with the best plan of action before proceeding with production and even the introduction of products to the market.
Here are few but key factors that explain the importance of testing materials in global manufacturing.
Meeting quality and regulatory standards
Ensuring that manufactured products are in line with international or industry standards is not merely a factor for a competitive edge, but a critical process to prevent or avoid the cause of damage and injury to consumers. Although it is important for all manufacturing industries, materials testing has the most vital role in maintaining safety in aircraft, infrastructure, military equipment, medical products, and all vehicles for the automotive market.
All manufacturing companies must adhere to the standards set by the government and regulatory bodies, and conduct their own testing procedures. There are also test standards such as ISO, ASTM, DIN, and more that ensure the quality of materials used and products made.
Selecting appropriate materials and treatments
Testing the quality of products is often done at the end of the manufacturing process to ensure if the products are well-made. However, it is also necessary to do materials testing at the beginning of the process in order to help manufacturers select the appropriate materials to be used for the product as well as identify which treatment is the most suitable for the creation and application of the product.
One specific reason as to why materials testing is necessary for selecting the appropriate materials and treatment is because many of the materials are mostly used in manufacturing such as metals, plastics, polymers, textiles, and composites exhibit Hookean behavior which means that the stress applied to stretch or compress a body is proportional to the strain or change in length produced. The performance of a structure is frequently determined by the amount of deformation permitted and manufacturers should be aware of the material’s capacity before proceeding with production.
Evaluating product design or specifications
When creating a new product design, it is only normal and necessary to test the materials to be used in order to ascertain their mechanical properties such as strength, hardness, elasticity, and fracture toughness.
Common testing capabilities include deformation strength, puncture strength, bend strength, tear and crush resistance, coefficient of friction, elastic limit, ductility, and compression. Corrosion testing is also done in order to determine if the material will hold up under certain conditions such as humidity or saltwater environment.
In further determining material characteristics, microanalysis, using microscopes and SEM equipment, can be used to analyze various surface features and to detect flaws and inconsistencies.
Verifying a production process
Last but not the least, it is important to remember that manufacturers would benefit from more efficient and productive operations. By doing materials testing during the product development stage and before committing to a planned production process, manufacturers can minimize errors during and after production, as well as save time and cost.
Materials testing also plays a huge role in failure analysis investigations because manufacturers would then have an idea about the possible causes of defective products. Ultimately, it is also a beneficial process for verifying if the material received from the supplier is really what was ordered and promised.
esting the materials to be used in production is more than just a manufacturing process for the global manufacturing industry; it is the responsibility of all EMS Company in the Philippines and other countries because aside from sales and company reputation, the safety of the consumers lies on the quality of the products.
Other Blog
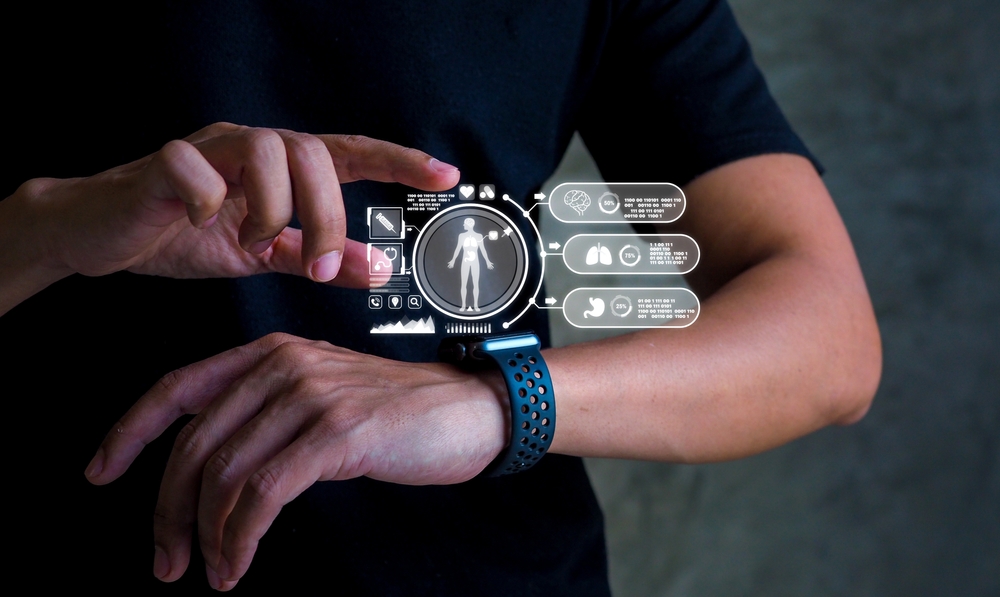
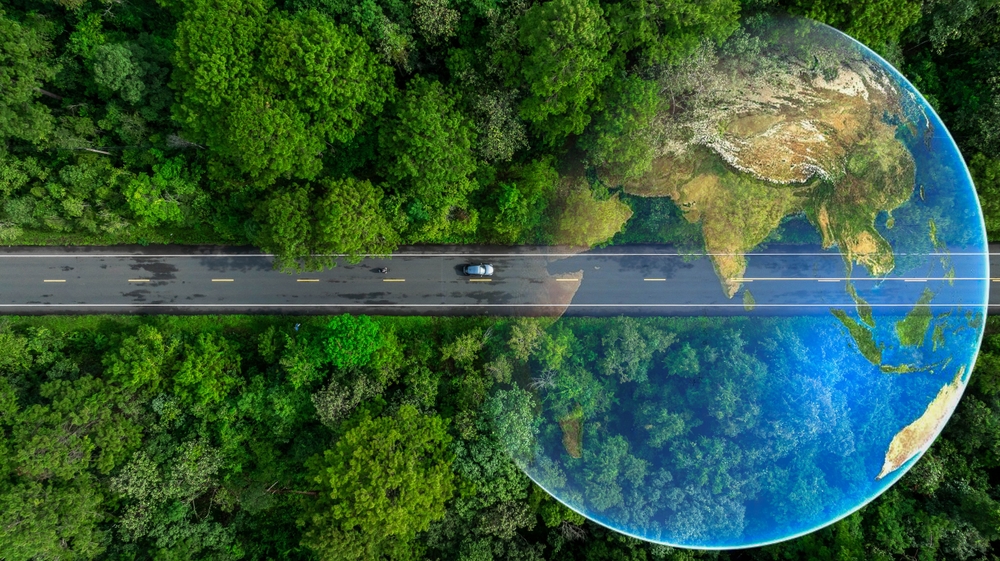
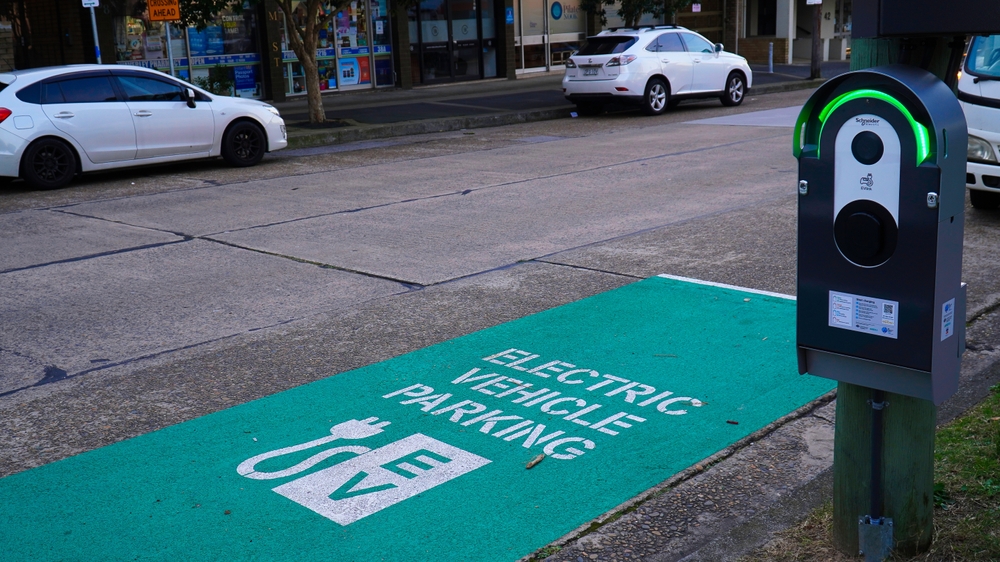