Industry 4.0: How to Make Manufacturing Future-Proof
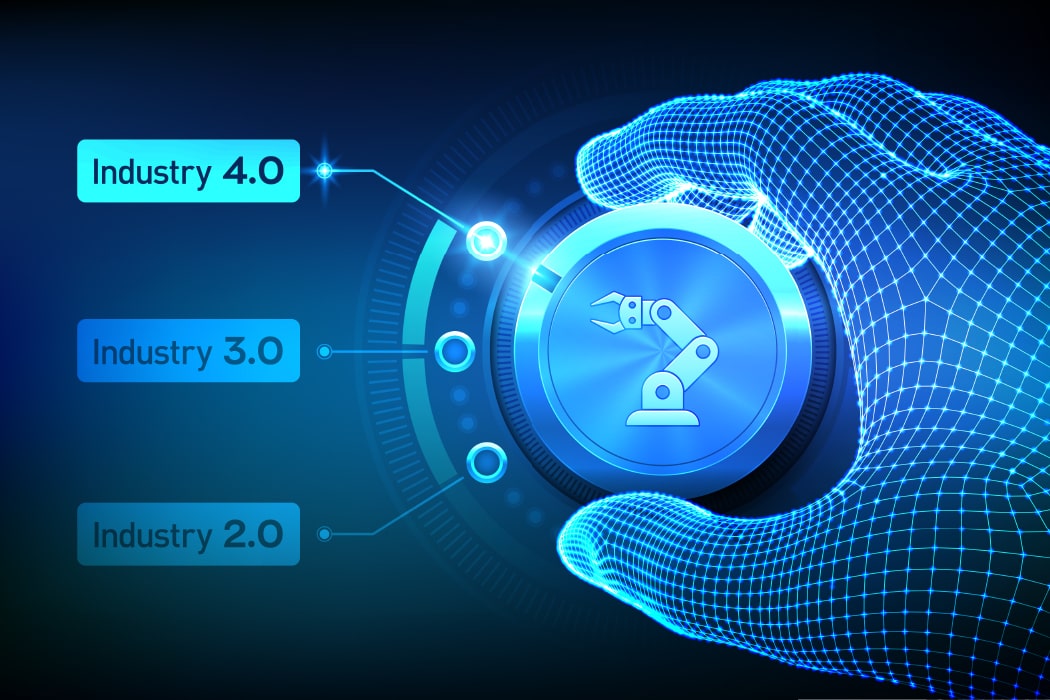
Industry 4.0 is crucial to sustaining business success through rapid market changes and adverse conditions. Is your business ready for the future?
If there is one lesson that we all learned in 2020, it’s that the world can change in the blink of an eye. Now, more than ever, the survival of a business depends on creating agility. To pivot and adapt to changing conditions, an open-minded, forward-thinking approach to technology is crucial.
In the race to future-proof industrial manufacturing, where do you stand?
We take a look at several industry surveys to discover the digital transformation strategies of global manufacturing companies. We’ll find out their future plans and priorities, as well as what technologies they are focusing on. We’ll also show how leading global companies are using digital technologies in their manufacturing facilities.
The future of manufacturing
In the COO Pulse Survey by PwC, global manufacturing executives from 585 large companies share their priorities and plans for the next one to two years.
Manufacturing technology today
Plex Systems, a software company that develops smart manufacturing platforms, surveyed 200 executives, business leaders, and professionals in operations, information technology, and engineering.
When asked about the status of their company’s Smart Manufacturing, Industry 4.0, or other industrial manufacturing programs, these were the results:
Digital factories around the world
According to Deloitte, 86% of American manufacturers believe that smart factories will be the main driver of competition by 2025. In addition, 83% think that smart factories will transform the way products are manufactured.
How are some leading global manufacturing companies harnessing technology to improve different areas of their operations?
Volkswagen Group
At its Chattanooga factory in the United States, engineers are using augmented reality (AR) goggles to design production lines and identify potential issues.
With this system, designers don't only see the individual parts of factory machinery--they also see how current and future equipment could interact in a real environment.
“This helps us to make decisions quicker, and spot potential issues sooner,” said Steffan Nunn, digital factory specialist at Volkswagen Chattanooga. “As we integrate new models into the existing factory, we need to make sure our virtual design data matches the reality in the plant.”
PepsiCo
The perfect chip is all about taste and texture. Frito-Lay, a subsidiary of PepsiCo, is using artificial intelligence (A.I.) and machine learning to deliver just that to its customers.
The company hits chips with lasers, using the sounds to determine texture. Algorithms process the sound to determine chip texture, automating the quality check of their processing systems.
Senior R&D Engineer Shahmeer Mirza also developed a machine learning model that, coupled with a vision system, could predict the weight of potatoes being processed. Mirza’s system helped the company save USD300,000 per line, which they no longer had to spend on weighing elements.
A custom-built engine monitors restaurant trends, social media, retail sales, and news and search analysis. Artificial intelligence maps out “flavor cycles” and predicts the staying power of a potato chip flavor. This information helps the company create new flavors. According to Fortune, A.I. has helped the company reduce its development process by 10%.
BMW
Described as a “factory of the future” by the World Economic Forum (WEF), the BMW Group plant in Regensburg, Germany, manufactured about 320,000 vehicles in 2018.
At Regensburg, more than 3,000 machines, robots, and autonomous transport systems are connected to the BMW IoT platform. Using technologies such as robotics, 3D printing, and smart data analytics, the plant was able to reduce quality issues by 5% and shorten the deployment time of new applications by 80%.
Here’s a video by CNN on BMW’s Regensburg factory.
https://edition.cnn.com/videos/business/2020/01/23/bmw-regensburg-smart-factory-biz-evolved-jlm-lon-orig.cnn/video/playlists/intl-business/
Lessons from smart manufacturing transformation leaders
To remain flexible and responsive to dynamic market forces, companies must adopt technology that connects people, machines, systems, and supply chains while also automating business processes and gleaning insights from big data.
But which technologies should you use, and how do you deploy them?
Deloitte conducted 40 qualitative interviews with manufacturing leaders, staff, and professional services providers who had firsthand experience with smart factory transformations. Here’s what they learned.
- Design based on real user needs. When designing smart factories, business leaders need to take a human-centered approach to “understand what [the user’s] pain points are, making sure we understand how they need to use information, what they need to look for, why they need to investigate it, and how they need to act on it.”
- Champion change at all levels. Executive-level support is crucial, given the resources required to transition to a smart factory. Senior leaders in operations, supply chain, strategy, and other functions can think strategically about how transformation can increase value. Those on the frontlines--operators, technicians, engineers, and managers--can drive change and results on the shop floor.
- Diversity fosters innovation and insight. Deloitte’s findings support research that the most successful transformations employ teams representing diverse functions and capabilities. These skill sets include engineering, information technology (IT), supply chain, production, master data management, analytics, user interface designers, and human resources, among others. Diverse mindsets should inform the overall approach, and the right skills should be deployed at the right time.
- Continuous support and learning. Adding and growing skills is crucial to the success of a smart factory. Building these skills ensures acceptance and adoption of technology solutions, provides support for staff as they adapt to new processes and systems, and creates a culture of constant learning.
“If we are to avoid playing catch-up when the next challenge hits--or the next opportunity appears--then we should be thinking now about what changes to our technology, processes, culture, and models can best prepare us for the future,” says applied futurist Tom Cheesewright.
By harnessing the right technology and employing these solutions in the right way, you will be able to deliver value to your business and solve challenges unique to your organization--now and in the future.
As one of the Top 20 EMS companies in the world, IMI has over 40 years of experience in providing electronics manufacturing and technology solutions.
At IMI, we believe that humanity drives technology, and we direct our passion at solutions that enhance our way of living. With more than 400,000 square meters of factory space in 22 factories across 10 countries, we are positioned to build your business on a global scale.
Our proven technical expertise, worldwide reach, and vast experience in high-growth and emerging markets make us the ideal global manufacturing solutions partner.
Let's work together to build our future today.
Other Blog
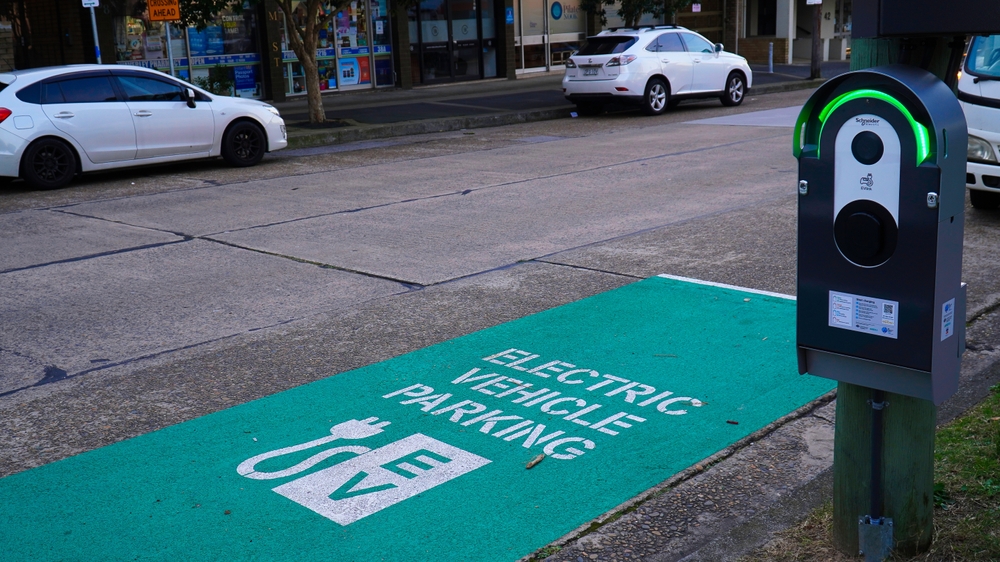
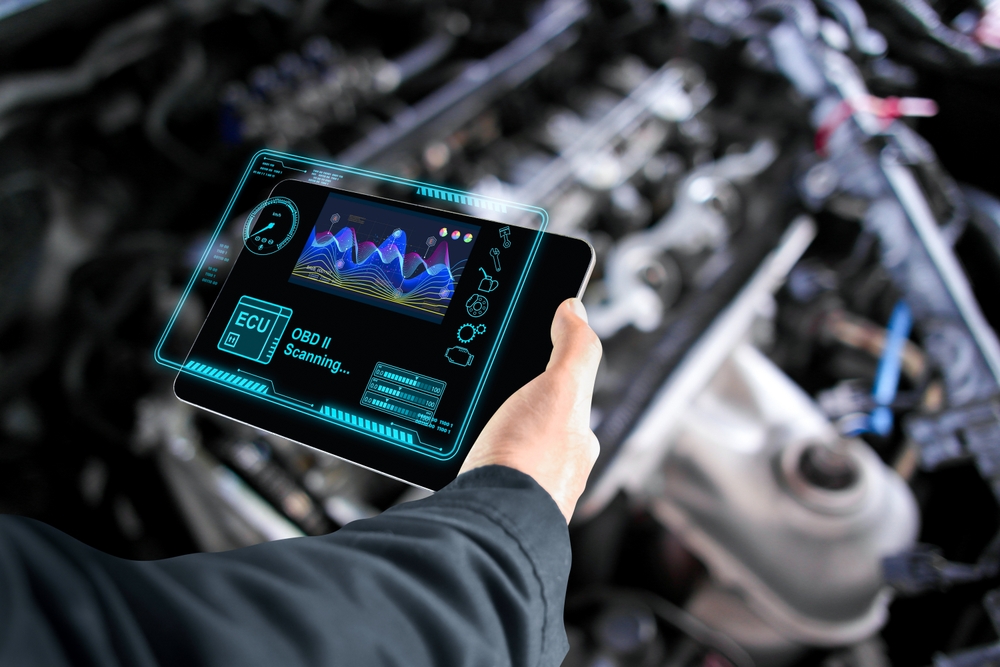