10 Advantages of Virtual Testing for EVs
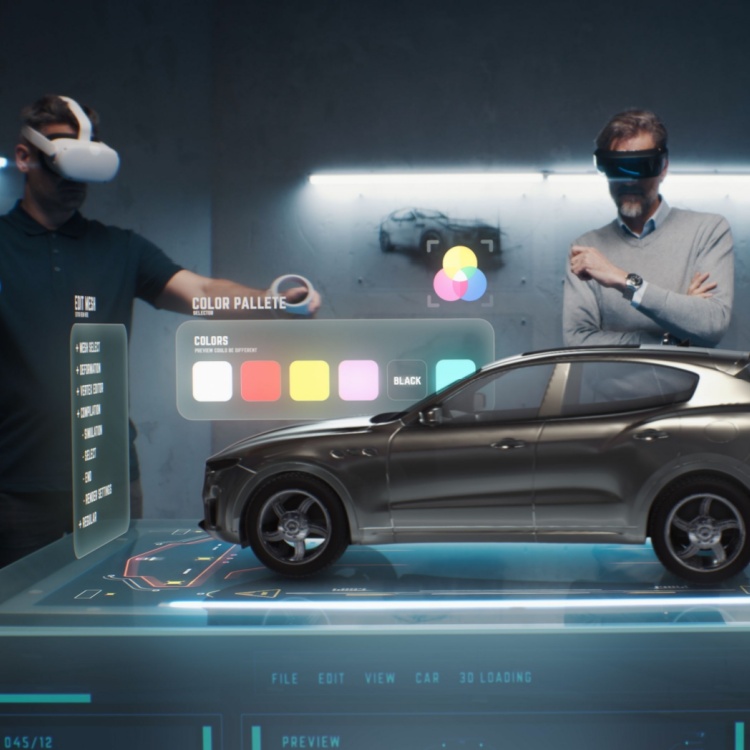
The global electric vehicle virtual prototyping market is projected to grow at a compound annual rate of almost 34% from 2021 to 2030. This surge underscores the transformative impact of electric vehicles (EV) on product design and development, driven by a focus on sustainability in the automotive market. However, these advancements also present unique engineering challenges, requiring innovative solutions to refine and optimize EV performance.
Dynisma, a UK-based motion simulator firm, offers manufacturing solutions with product testing tools. By minimizing the use of physical prototypes, the company states that car manufacturers can save over $10 million per model. Its Dynisma Motion Generators (DMGs) deliver virtual yet realistic driving experiences with swift feedback and seamless data processing.
Developing a new vehicle often requires over 50 prototypes, each costing around $500,000, making physical testing a significant expense for automakers. However, modern driving simulators like the DMGs can reduce the need for prototypes by 40%, offering substantial cost savings in the development process. These simulators improve mechanical and reliability testing, further optimizing vehicle design for manufacturing efficiency.
10 benefits of virtual prototyping for EVs
Virtual prototyping, powered by artificial intelligence (AI), creates detailed models to simulate system behavior and visually predict performance in practical conditions. In the age of electric transportation, this technology has become a vital testing solution. We explore why virtual prototyping is crucial for the future-proof development of electric vehicles.
-
Shorter timeline
Virtual prototyping enhances engineering capabilities by producing efficient digital models, reducing development timelines and expenses. This approach integrates design, simulation, and analytical testing, enabling rapid iteration and performance feedback. Engineers can explore countless scenarios and optimize designs effortlessly. Dynisma maintains that its simulators exemplify this innovation by streamlining processes and potentially reducing time to market by 50%.
-
Cost savings
Virtual prototyping for EVs reduces costs by eliminating the need for expensive physical prototypes. It improves operational efficiency by reducing reliance on manpower and materials in manufacturing engineering. By streamlining design and testing, companies save resources while optimizing processes. Additionally, faster validation enables quicker market entry, allowing manufacturers to recoup investments sooner and remain competitive. This cutting-edge approach not only lowers development expenses but also enhances productivity and supports cost-effective, high-quality electric vehicle production.
-
Flexible testing environment
Virtual testing provides engineers with a rapid platform for test and system development in EV design. By simulating real-world conditions like extreme temperatures and terrain, engineers can conduct detailed thermal analysis, evaluate mechanical systems' motion behavior, and assess durability. Virtual tools also allow for precise visual inspection of components, ensuring quality before physical prototypes are created. Moreover, virtual environments offer flexibility, enabling engineers to modify scenarios and iterate designs without time and cost constraints.
-
Refined designs
A primary advantage of virtual testing for EVs is the ability to explore and fine-tune various design options, improving system efficiency. Traditional methods often reveal design flaws too late, leading to delays and higher expenses. Virtual testing allows for earlier identification and resolution of issues, enabling continuous feedback and adjustments. While physical tests provide data, they may miss crucial details for design perfection.
-
Standard compliance
Virtual EV prototypes ensure standard compliance by enabling engineers to conduct thorough simulations and scenario-based testing over an extended period. This allows for early validation of safety, performance, and efficiency requirements. Given the complexity of self-driving and modern vehicle systems, virtual simulations are crucial for validating algorithms and components like steering and braking. Furthermore, virtual prototyping supports production line validation, ensuring precision machinery operates optimally and facilitating a smooth transition from design to manufacturing.
-
Holistic evaluation
Virtual prototyping provides a holistic evaluation of an EV’s performance by integrating powertrain efficiency, battery performance, and functional safety. This approach allows teams to analyze the impact of different powertrain architectures on driving range and assess battery designs’ effect on overall efficiency. Additionally, functional safety teams ensure control systems meet required standards. Virtual testing supports the enhancement of all vehicle components, improving the product life profile and ensuring long-term performance and reliability.
-
Keeping pace with the growing demand
As the automotive industry shifts towards EVs, manufacturers face increasing pressure to scale production quickly. By 2040, EVs will make up 54% of all new car sales globally, a trend driven by significant improvements in battery technology, lowering EV prices, and the growing adoption of clean energy policies worldwide. By leveraging digital tools, automakers can better manage supply chain constraints while keeping up with the rapidly evolving EV market.
-
Boosted safety
Safety testing in real-world scenarios can be both risky and costly. Virtual prototypes enable the simulation of hazardous situations, such as crash tests and extreme conditions, without endangering lives. These help refine vehicle safety systems by providing valuable data on how components react under stress. Additionally, virtual testing can assess a range of scenarios, ensuring a thorough evaluation of safety features before physical testing, improving the overall safety design of electric vehicles.
-
Smaller carbon footprint
Using digital simulations instead of physical prototypes for electric vehicles offers significant environmental advantages. By reducing the need for material production, transportation, and physical testing, automakers lower resource consumption and emissions. Digital models eliminate waste associated with discarded prototypes while cutting down on energy use and travel-related carbon emissions. This approach aligns with the automotive industry's goal of sustainability, helping to create greener, more energy-efficient production processes that contribute to a smaller overall environmental footprint.
-
Enhanced Collaboration
Virtual prototyping fosters collaboration across various teams, ensuring seamless communication throughout the development process. Engineers, designers, and safety experts can simultaneously interact with digital models, providing valuable feedback and adjustments in real-time. This collaborative approach allows for more efficient problem-solving and decision-making, as all stakeholders can access the same data. By streamlining teamwork and breaking down silos, virtual prototyping enhances cross-disciplinary integration.
Virtual prototyping plays a crucial role in shaping the future of electric vehicles. By creating accurate digital models, manufacturers can test designs, improve performance, and reduce the need for physical prototypes, saving time and resources.As one of the Top 20 EMS companies in the world, IMI has over 40 years of experience in providing electronics manufacturing and technology solutions.
We are ready to support your business on a global scale.
Our proven technical expertise, worldwide reach, and vast experience in high-growth and emerging markets make us the ideal global manufacturing solutions partner.
Let's work together to build our future today.
Other Blog
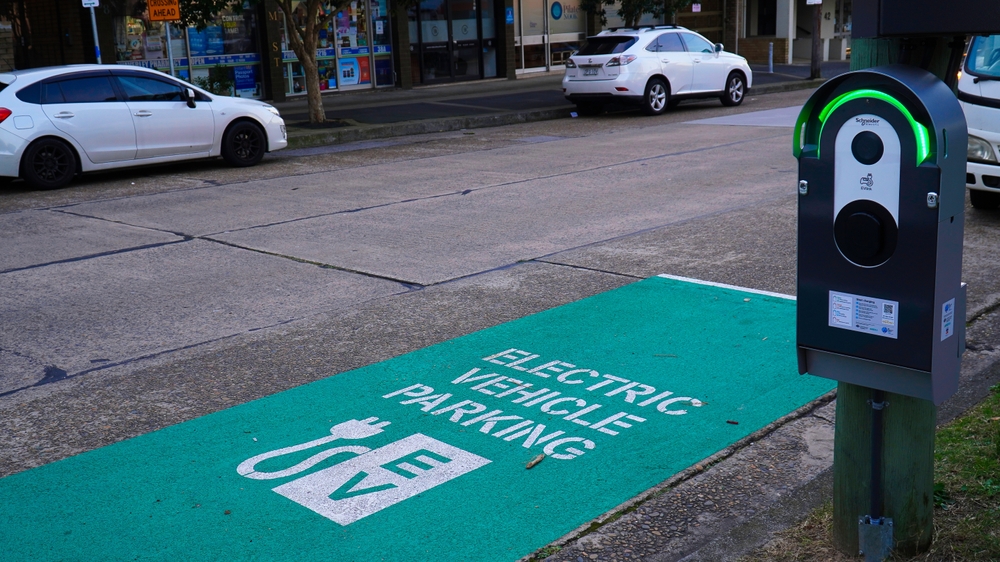
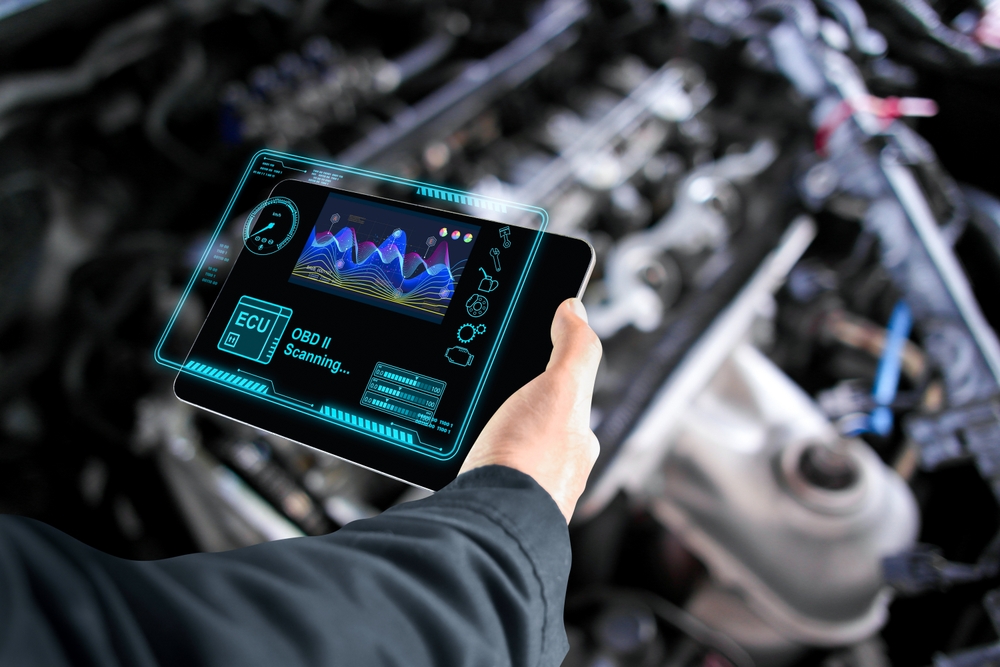