You Can Overcome These 10 Manufacturing Challenges
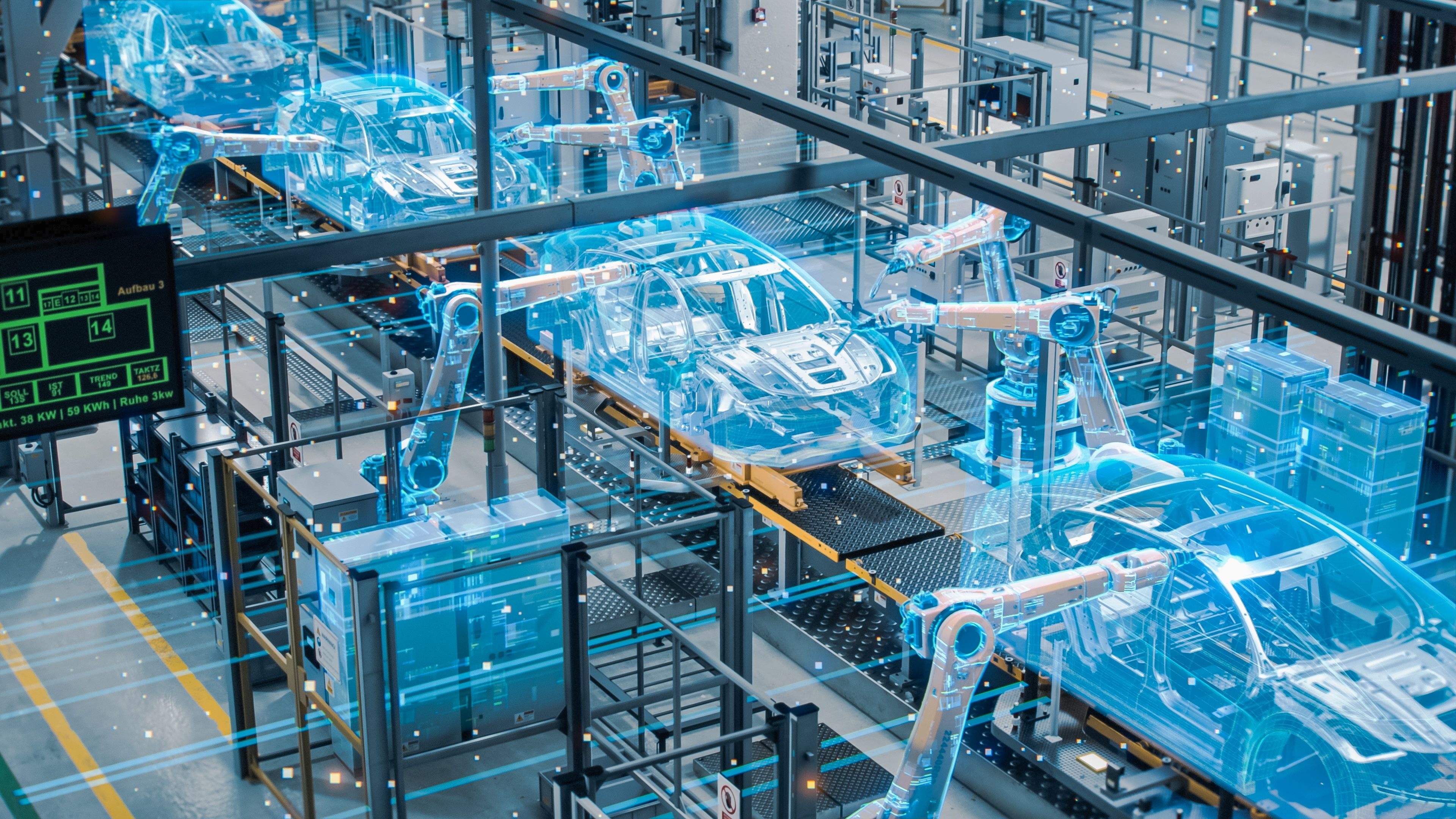
Automation, artificial intelligence (AI), and machine learning are all manufacturing solutions that can improve operational efficiency, sustainability, and supply chain management. The pandemic fast-tracked digital transformation, as off-site work and decentralized production emphasized the need for connected and flexible system development. Yet, why are many manufacturers still hesitant to adopt tech advancements?
The overall contract manufacturing market is projected to reach $0.75 trillion in 2025, expected to grow to $1.12 trillion by 2030, reflecting an impressive 8.7% compound annual growth rate during the forecast. This growth highlights the increasing demand for contract manufacturing solutions, as businesses seek cost-effective and efficient ways to produce goods while focusing on their core operations.
To maximize this growth, manufacturing technologies and industries are evolving with key trends shaping their future. Companies are investing more in digital threads to integrate data and improve efficiency. Environmental, social, and governance (ESG) practices are becoming a priority as businesses prepare for regulatory shifts that could impact costs.
There is also a growing focus on generating measurable returns from software investments to enhance user experience. Mergers and acquisitions are becoming more strategic, not just for cost savings but to expand capabilities, skills, and technology. Additionally, businesses are strengthening supply chains to be more resilient and adaptable after the disruptions caused by the global pandemic.
(Also read: Factories Made for the Future)
10 challenges slowing tech adoption in manufacturing
Global manufacturing is facing uncertainty, with multiple challenges disrupting the industry. Rising inflation, recession risks, supply chain issues, and global conflicts create economic pressure. Additionally, the future of globalization is uncertain, as regional interests may take priority, leading to a more divided global market.
Modernizing technology is key to keeping industrial manufacturing agile and competitive. The challenge isn’t the technology itself but how well companies use it. Many struggle with future-ready upgrades not because of hardware or software but due to internal obstacles that slow down progress in planning, building, and deploying the right tech infrastructure.
Here are our top 10 risks that keep manufacturers from investing in technology:
-
Fear of cyber risks
As manufacturers connect more devices and integrate IoT systems, outdated security makes them vulnerable to cyberattacks. These breaches can cause disruptions, loss of information, and financial harm, sometimes even halting production entirely.
To deal with these risks, manufacturers should use test solutions like vulnerability assessments and penetration testing, implement multi-factor authentication, train employees, and ensure security measures are adaptable as operations expand.
-
Lack of a unified IT approach
A major obstacle to digital transformation is poor system integration. Without a unified IT strategy, disconnected systems cause inefficiencies, security issues, and conflicting goals, hindering data and process alignment across departments.
Solutions include auditing existing systems to identify gaps, implementing a centralized data system for real-time access, fostering cross-departmental collaboration, and using change management to ensure smooth transitions and increased adoption.
-
Significant expenses
High initial costs and ongoing expenses, including software, training, maintenance, and upgrades, prevent manufacturers, especially smaller ones, from investing in advanced technologies, risking financial strain and delayed returns.
To address high costs, manufacturers can adopt lean manufacturing to reduce waste, implement modular systems for scalable upgrades, and explore financing options or partnerships to share the financial burden. These strategies help manage expenses and make technology investments more feasible.
-
Downtime during implementation
New technology installations can cause production downtime, leading to revenue loss, supply chain delays, and workforce productivity issues. Poor planning and extended transitions may reduce the expected benefits of the investment.
Instead of implementing new technology all at once, manufacturers can roll it out in phases, schedule upgrades during low-demand periods, run parallel systems, partner with experienced vendors, and conduct analytical testing for effective product validation.
-
Slow adoption of automation
In the industrial market, 44% of businesses lack automation, leading to unchecked human errors. More than a third fail to incorporate security into operations, leaving them vulnerable to disruptions.
Complete modernization requires expertise in change management, skill development, and system integration. IT leaders can choose to collaborate with trusted experts to bridge skill gaps, provide innovative solutions, and improve cybersecurity for long-term success.
-
Outdated legacy infrastructure
Outdated IT infrastructure hampers manufacturers' ability to integrate new technologies, leading to inefficiencies, higher maintenance costs, and security vulnerabilities. This resistance to modernization slows tech adoption and limits growth potential.
According to McKinsey, companies hurdle this challenge by investing heavily in cloud technology, driving higher profit margins. Additionally, strong financial operations help manage cloud spending by providing better visibility, resource tracking, and forecasting.
-
Skills gap
The lack of technical expertise prevents the effective adoption of new technologies. According to a survey, nearly 42% of respondents stated that their organization doesn’t possess the skills to manage their existing operating model.
Building a skilled talent pool is a challenge for many companies. McKinsey states that successful companies invest in reskilling and development, focusing on cloud and cybersecurity roles to drive transformation.
-
Unpredictable returns
Manufacturers hesitate to invest in technology due to unpredictable returns. With unclear financial benefits and the risk of delayed outcomes, companies are cautious about adopting innovations like automation, AI, and advanced systems.
High-performing organizations excel at executing transformation initiatives, realizing business value, and focusing on cybersecurity, talent, and technology strategies. While investing in infrastructure, they see increased revenue and cost reduction from tech-driven improvements.
-
Traditional operational mindsets
The siloed mindset in operations limits cross-department collaboration, creating resistance to change. This fragmentation makes tech adoption difficult, as departments struggle to align on goals, slowing down innovation and investments.
Overcoming siloed mindsets requires fostering collaboration across departments, promoting shared goals, and implementing integrated systems. By encouraging open communication and breaking down barriers, manufacturers can make more effective and cohesive tech investments.
-
Evolving customer preferences
Customer expectations, such as faster delivery, customization, and seamless experiences, can overwhelm manufacturers. The fear of not keeping up with these expectations or making the wrong tech investments often leads to hesitation.
For instance, original equipment manufacturers (OEMs) often lack customer insights beyond product serial numbers, making it difficult to address client lifecycle needs. To enhance product design and development, manufacturers must engage with customers for maintenance, new features, and replacements.
Technology plays an essential role in the future of manufacturing, driving efficiency, innovation, and competitiveness. As the industry evolves, embracing digital transformation is crucial for businesses to overcome challenges, enhance operations, and remain ahead in the market.As one of the Top 20 EMS companies in the world, IMI has over 40 years of experience in providing electronics manufacturing and technology solutions.
We are ready to support your business on a global scale.
Our proven technical expertise, worldwide reach, and vast experience in high-growth and emerging markets make us the ideal global manufacturing solutions partner.
Let's work together to build our future today.
Other Blog
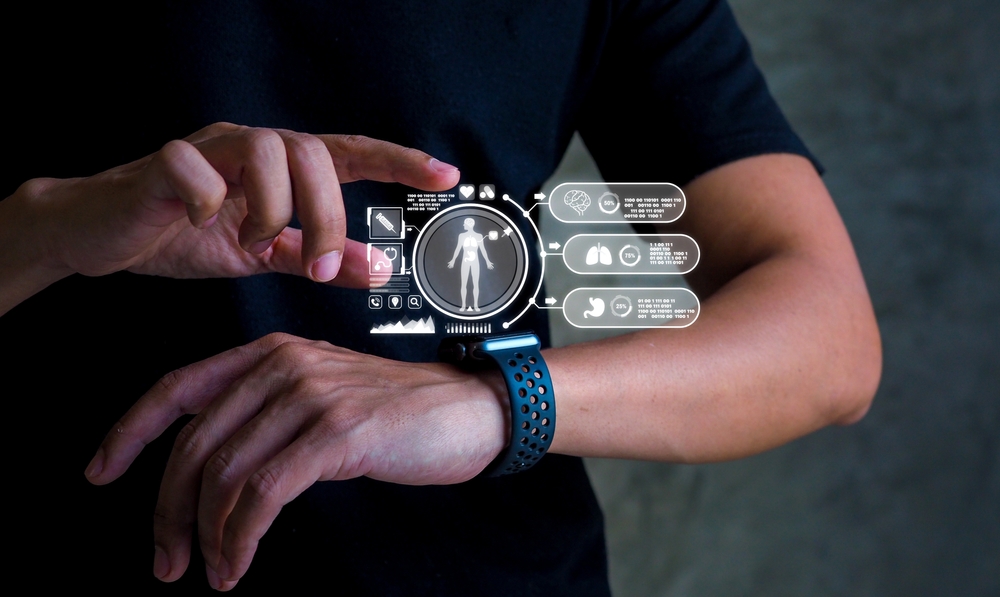
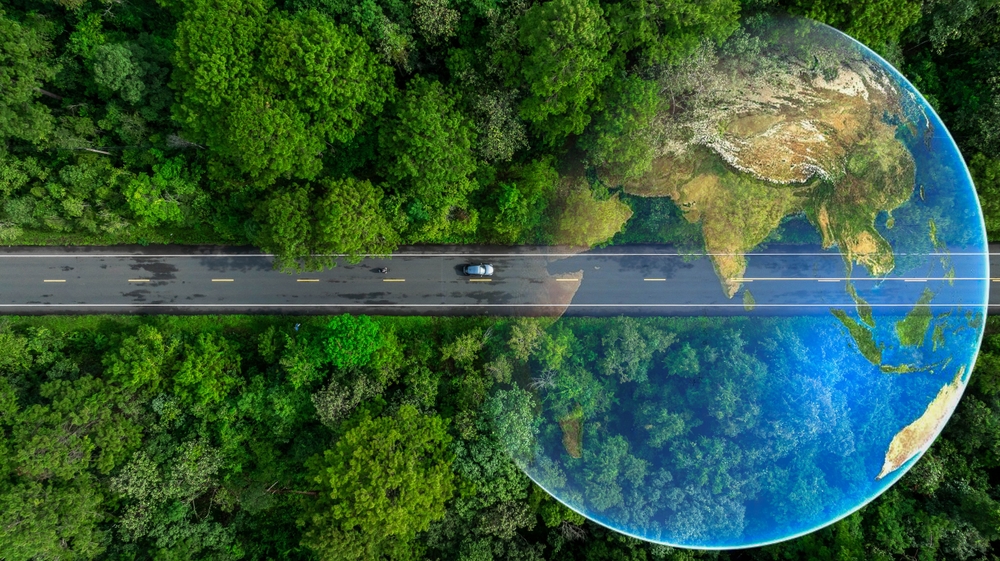
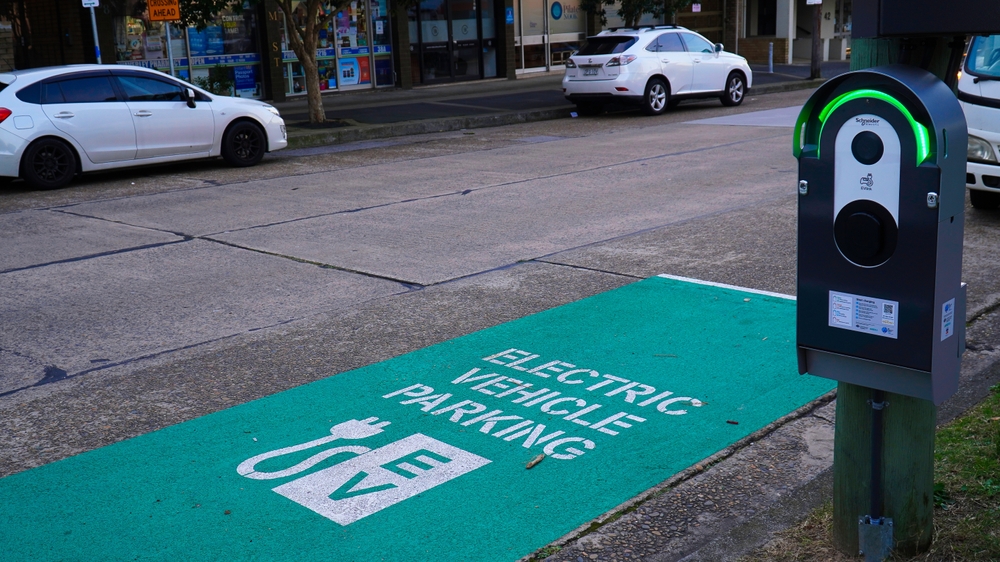